Key takeaways
- Assemble-to-order (ATO) is a lean manufacturing strategy.
- ATO seeks to lower carrying costs, which are overhead costs associated with holding inventory/materials.
- ATO can lower both carrying costs and labor costs.
- Not every product is suitable for an assemble-to-order manufacturing strategy.
- Generally speaking, mid-to-high cost products with limited customization are suitable for ATO.
You have to spend money to make money. It sounds like an oxymoron– and a cliche one at that– but it’s true. And no one understands that better than businesses. Overhead costs account for a large part of their expenditures. Of these expenses, inventory carrying costs account for a large portion. That’s why manufacturers use methods like assemble-to-order (ATO) to reduce their carrying costs and increase their profit margins.
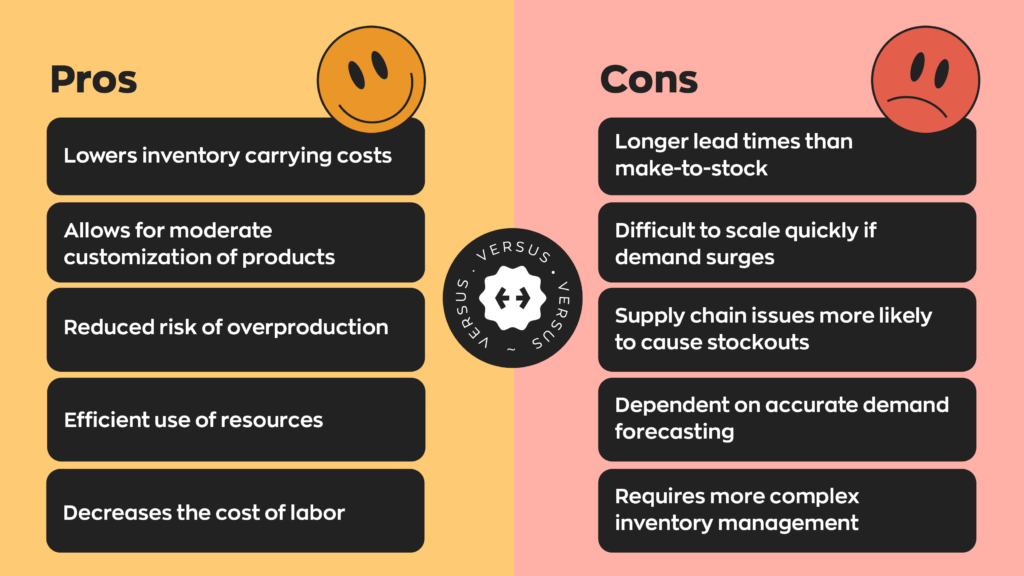
Assemble-to-order manufacturing is a process that offers a unique balance between customization and rapid fulfillment. It can reduce carrying costs while delivering tailored solutions to customers if used properly.
In this article, we’ll explore how ATO manufacturing works, its benefits and challenges, and how manufacturers can leverage this strategy to stay competitive.
What is assemble-to-order manufacturing?
The ATO meaning is, for the most part, exactly what it sounds like. Instead of assembling many identical units all at once, manufacturers assemble them to the customer’s specifications after the order has been placed. This is noticeably different from make-to-stock (MTS) strategies, where businesses assemble products ahead of time to match demand.
There is also the make-to-order strategy, which involves manufacturing the individual components once the order has been received. This may sound similar to assemble-to-order, but MTO usually involves a high level of customization, while ATO is more limited.
For example, let’s say you own a computer store specializing in customized computer systems for small businesses. Customers can choose different configurations, such as processor type, memory, storage options, and graphics cards. To fulfill your orders quickly, you keep an inventory of pre-built components (motherboards, hard drives, RAM, etc.) in stock.
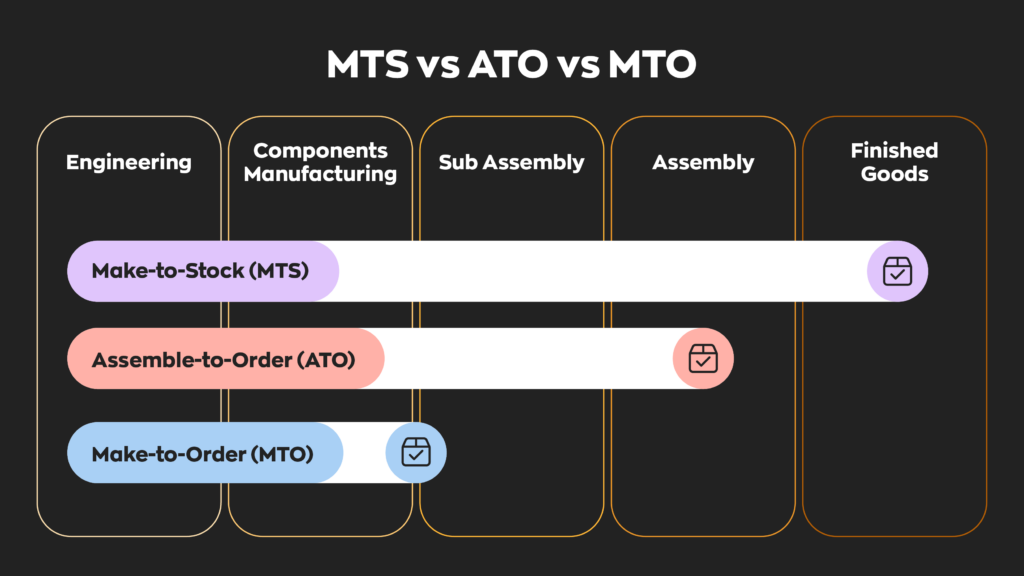
When a customer orders, you assemble the system using the chosen components and ship it within a few days. This process is quick and flexible since the core parts are already in inventory. This is a classic example of assemble-to-order. The order triggers the final assembly, but most of the work is already done by stocking the pre-manufactured parts in advance.
What are the benefits of assemble-to-order?
Adopting an assemble-to-order strategy has quite a few benefits. The two main ones are reducing the amount of necessary stock and labor costs. We’ve talked about lean manufacturing before, and you can think of it in a similar way.
Assembling products all at once requires a lot of labor and a large number of components. Like lean manufacturing, assemble-to-order strategies seek to lessen that cost and spread it over a longer period.
Only assembling units after receiving an order will directly reduce the required manpower. This is a big deal, considering labor can account for up to 70% of business costs. Having just a few assembly lines for a few product variations is less labor-intensive than mass assembling units.
It also directly cuts down on the amount of necessary materials. Inventory costs account for a large portion of business costs. Not only are there acquisition costs, but there are also warehouse fees, maintenance costs, and even tax implications. Keeping your stock levels low will save you a ton on these expenses.
The downsides of assemble-to-order manufacturing
Despite the many benefits of ATO manufacturing, this process is only viable for some businesses. For example, high-demand, low-cost products, like reusable water canteens, would not benefit from an assemble-to-order manufacturing process.
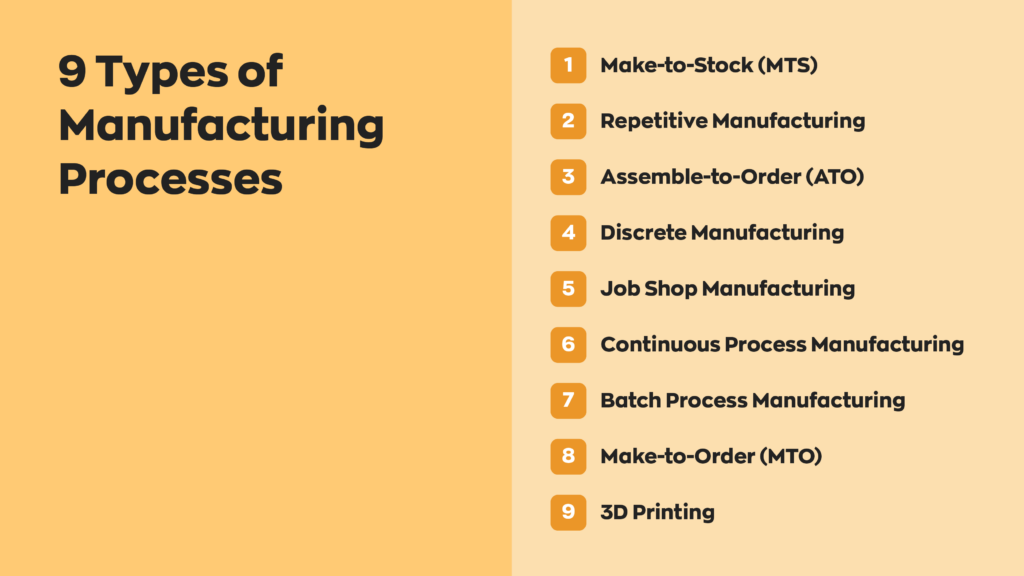
Another major drawback of assemble-to-order is the slight delay between buying and receiving an order. For some consumers, waiting longer before receiving their order is unacceptable, especially in the new age of fast-paced ecommerce.
It’s also worth mentioning that since assemble-to-order manufacturing blends the properties of both make-to-order and make-to-stock, it’s susceptible to the problems of both. Nevertheless, assemble-to-order strategies still rely on forecasts—just not as heavily.
Assemble-to-order best practices
Implementing an ATO process takes time and generally requires some number-crunching to keep things running smoothly. Here are some best practices to keep in mind while implementing an assemble-to-order manufacturing process.
Select suitable products
We mentioned it already, but it’s worth repeating: ensure the product is suitable. It doesn’t need to be your only product or even your main product. An assemble-to-order workflow doesn’t need to be business-wide, but if it doesn’t make sense for the product, there’s no point. As a good rule of thumb, somewhat customizable mid-to-high-price products are suitable for assemble-to-order systems.
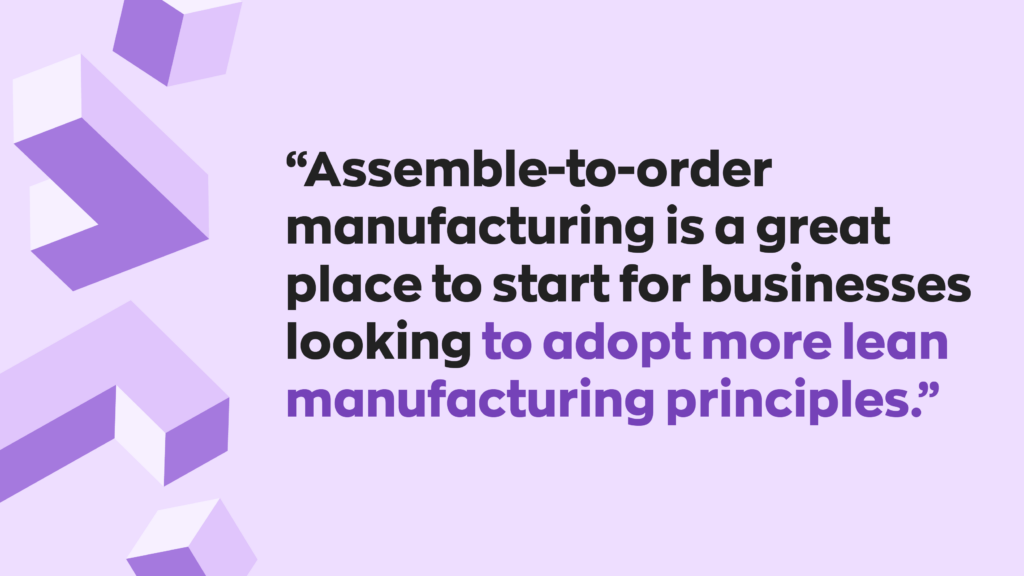
Monitor demand
Assemble-to-order relies heavily on accurate forecasts to meet demand while avoiding overstocking. That means it’s imperative that you monitor your demand closely and ensure that you order the perfect balance of components. Leveraging your historical data is also a great way to improve your demand forecasting, so take advantage of any analytics at your disposal.
Segment the manufacturing process
Breaking the manufacturing process down into different stages can help reduce the delay between an order and delivery. For instance, let’s go back to our computer store example. Rather than assembling every computer component with each order, you could put some subassemblies together beforehand. This will dramatically speed up the assembly process and allow you to deliver your products swiftly.
Use manufacturing software when possible
Automation is a big part of modern business, and manufacturing software is the cheapest way to start automating. Robust software like inFlow has features like bill of materials (BOMs) and subassemblies that are essential for any manufacturing business. It also has everything else you would expect in inventory management software, like real-time inventory tracking, reorder points, purchase orders, and sales orders. And did we mention barcodes? Well, inFlow has those, too!
Wrapping up
Assemble-to-order manufacturing is an excellent solution for businesses looking to balance customization and cost efficiency. By adopting an ATO workflow, manufacturers can reduce inventory carrying costs while still providing tailored options to their customers. However, assemble-to-order isn’t a one-size-fits-all approach.
Businesses should carefully select suitable products, monitor demand, and use automation tools whenever possible to make the most out of assemble-to-order manufacturing.
0 Comments