In the fast-paced world of inventory management, the pressure is always on. Inventory managers are responsible for juggling multiple tasks like managing stock levels, purchasing inventory for replenishment, and optimizing warehouse space. With so much to worry about, it’s all too easy for people managing inventory to find themselves experiencing severe burnout if they don’t manage their tasks correctly.
So, for the sake of your sanity, today we will talk about how you can improve your inventory management game and avoid burnout by implementing processes that will help you improve and automate your workflow. Let’s dive in!
What is burnout, and what causes it?
We’ve all experienced burnout at some point in our professional career. Prolonged periods of work that leave you exhausted either mentally, physically, or both can cause burnout. This state can make it difficult to continue working efficiently and make people more prone to errors.
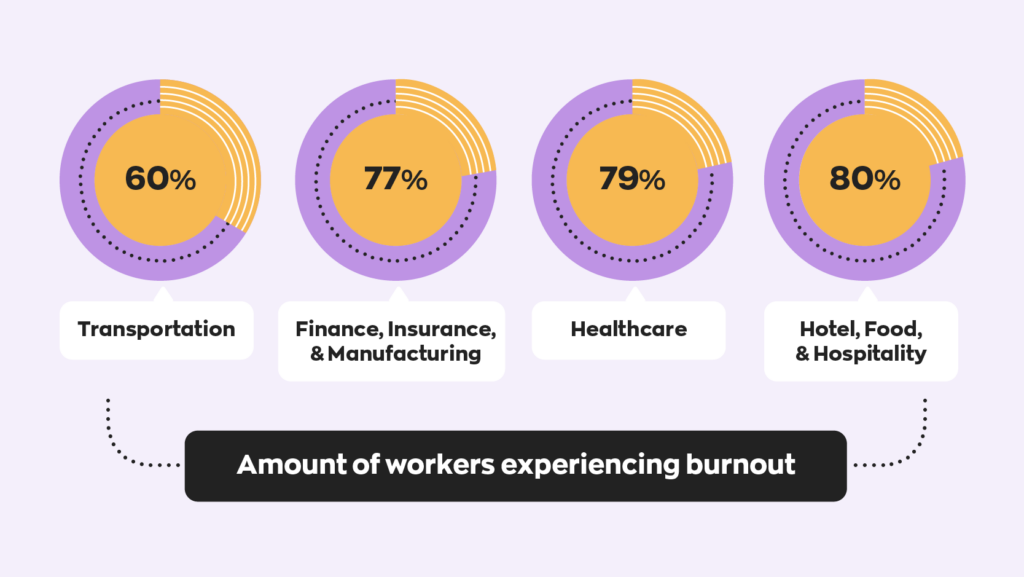
When it comes to managing inventory, the constant need to meet tight deadlines, maintain accurate stock levels, or deal with unexpected supply chain disruptions can easily result in burnout. All these factors can make it challenging to avoid burnout unless you have the correct processes in place.
How can burnout impact inventory management?
As mentioned above, a lot goes into managing inventory, and one small mistake could cause a domino effect throughout your entire business.
For example, let’s say you’re managing inventory for a small manufacturing business. One of your many tasks is maintaining inventory levels to ensure the assembly lines operate uninterrupted. However, it’s the peak of your busiest season, and you’re incredibly overworked. Burnout is starting to set in, and in the fog of your exhaustion, you mistakenly entered an extra zero in your inventory spreadsheet. This simple error abruptly caused the factory to run out of an integral component. Now, you have no choice but to shut down all the assembly lines until you can replenish the necessary stock.
It’s easy to see how one small mistake can cause a ripple effect throughout an entire organization. And the results can be costly, sometimes catastrophic for business owners.
Tips to avoid burnout when managing your inventory
Experiencing burnout from managing your inventory doesn’t have to be inevitable. In fact, with the right systems and processes in place, you can avoid it altogether. Here are a few strategies you can implement when managing your inventory that will help you eliminate burnout.
Embrace Automation
Using modern technology is the easiest way to quickly improve your inventory management. And by this, we don’t mean upgrading from pen and paper to Excel spreadsheets. With the right technology, you can automate tedious tasks that will free you up for more important things.
Our software inFlow is loaded with features that help automate processes when managing your inventory. For example, a popular feature of our software is the ability to set reorder points. With this feature, you’ll get a notification when your inventory dips below a certain level, prompting you to reorder more. And with our built-in barcode system, you’ll save loads of time on manual data entry. Not to mention preventing countless errors during the picking process.
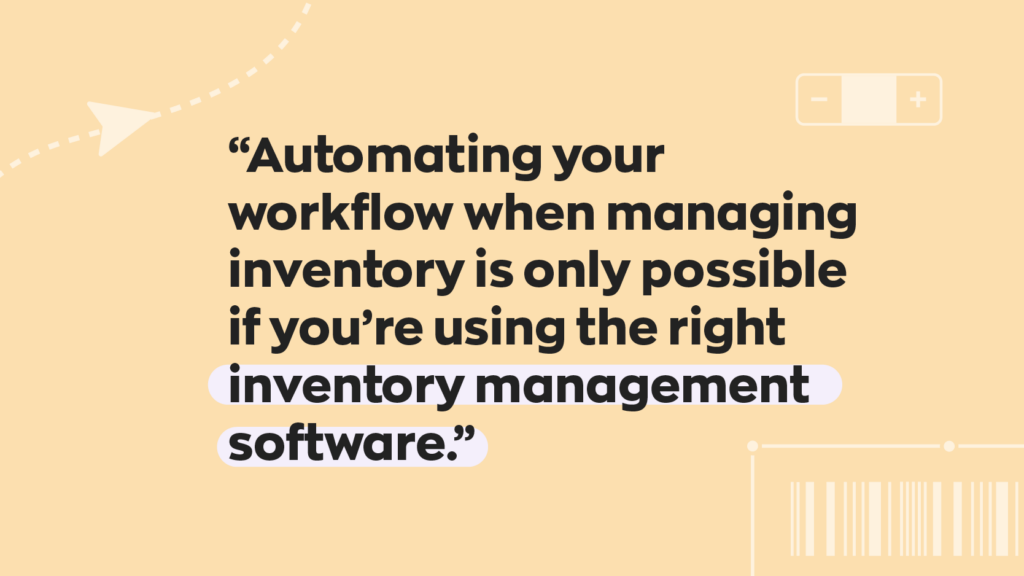
Prioritize your tasks
When managing your inventory, not all tasks are created equal. Fulfilling orders and replenishing stock will inevitably take precedence over reorganizing your warehouse space. It’s best to organize your tasks into two categories: high priority and low priority.
Once you’ve made these distinctions, deciding the best use of your time will be easier. Always be sure to complete high-priority tasks first before starting on any low-priority ones. Otherwise, you may find yourself scrambling and putting in extra hours to make up for lost time.
Delegate whenever possible
As much as we all wish it were possible, we can’t do everything ourselves. We’ll inevitably need to rely on others to make meaningful strides in our business operations. However, not all tasks can or should be delegated to others when managing your inventory.
The first step for proper delegation is to identify the things in your workflow that only you, the inventory manager, can do. You should outsource anything else to other employees. However, be sure to give these duties to someone with the time for them. Delegation is about creating a balance of duties and responsibilities for everyone.
Train your employees
If you want to maximize your time you need to figure out a way to effectively carry out daily tasks as quickly as possible. Doing this will take a lot of trial and error, which means a substantial time investment. This is why so many successful businesses implement standardized processes. What does this mean? Since you’ve already spent considerable time identifying how to quickly and effectively carry out a task, you can train new employees using this information, eliminating the learning curve. This type of employee training will save time for everyone across the board.
Outsource managing your inventory
Sometimes, even delegating within your organization has its limitations. After all, you don’t want to start delegating to avoid burnout only to cause your employees to burnout instead. If everyone on your team feels overwhelmed, it’s probably best to consider outsourcing.
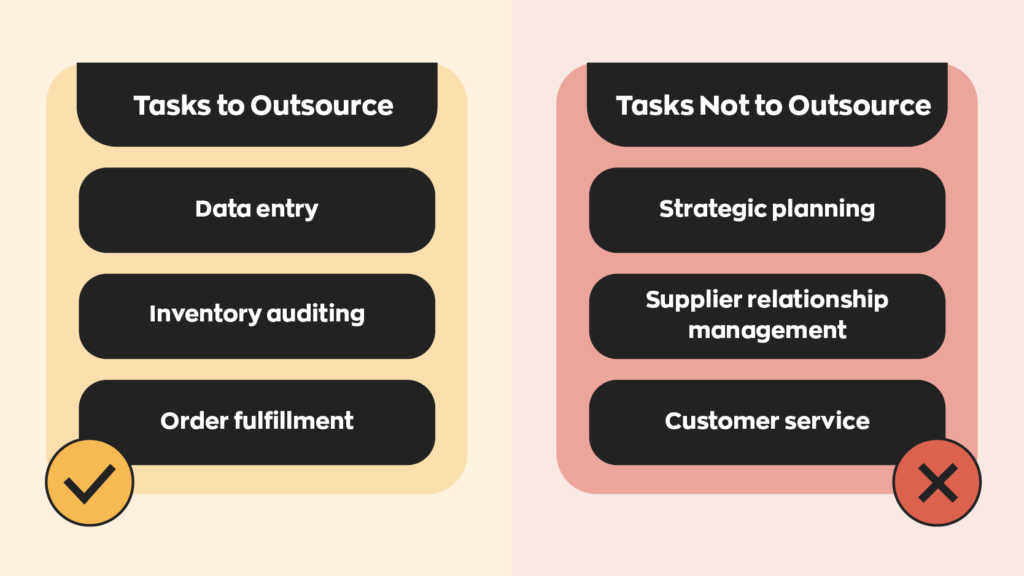
There are numerous 3PL companies available that can assist in managing your inventory. Of course, as with anything, there are pros and cons to going in this direction. Most notable would be the loss of control you’ll have over your inventory.
Foster a healthy work culture
Avoiding burnout starts at the top. Those in charge decide what’s expected of their workers. If the person in charge of managing your inventory is you, then the responsibility of creating a healthy work culture falls on your shoulders.
This means putting realistic goals in place that are actually achievable. Otherwise, your workers will quickly burn out trying to meet these impossible standards. No matter how refined your processes are, you’re setting your team up for failure if you set unrealistic goals.
Workplace success is all about work-life balance. Foster an environment where your employees can do their best work daily but also have the flexibility to take a walking holiday in Italy to unwind without being reprimanded.
Conclusion
It’s easy to fall into the trap of thinking that burnout happens to everyone, especially people managing inventory. But it doesn’t have to be that way. You don’t have to be bogged down by grueling manual data entry or messy spreadsheets. These things cause burnout, eat up your time, and hurt your bottom line.
With the proper process and systems in place, you can easily avoid burnout and create a healthy work-life balance. The time commitment needed to implement these new processes may seem a bit overwhelming, but the payoff will be well worth it.
0 Comments