Key takeaways
- Barcodes for manufacturing have various benefits, such as improved shipping and receiving, end-to-end traceability, better equipment management, and cost tracking.
- Manufacturers should only consider GS1 barcodes for finished goods
- You can create free, custom barcodes for internal tracking of components and assets.
- Flexible barcode creation options include barcode fonts, generators, or integrated software.
- A functional barcode system requires barcodes, a scanner, a printer, and software.
We may not realize it, but behind the scenes, barcodes play an essential part in our everyday lives. They’re a vital part of the global supply chain, ensuring the smooth flow of goods from the beginning of the product journey til the end. It’s not an exaggeration to say that the supply chain would simply not function as efficiently as it does today without barcodes.
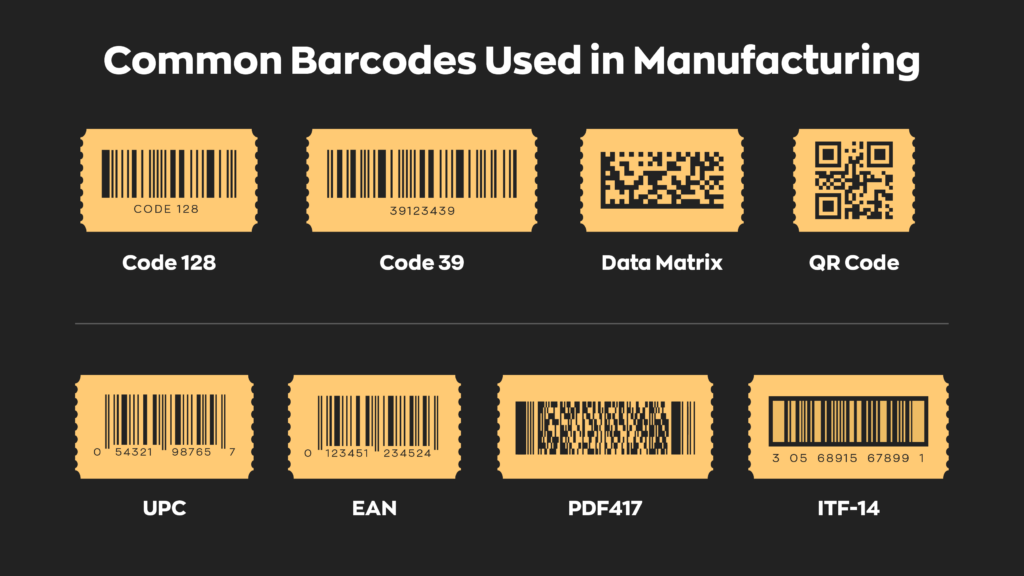
While it’s true that most businesses can benefit from adopting barcodes, manufacturers, in particular, stand to benefit the most. But why is that? And what should you, as a manufacturer, keep in mind when implementing barcodes for manufacturing?
Why are barcodes for manufacturing important?
Simply put, manufacturers use barcodes for more things. For example, retailers typically use barcodes to track product stock levels and inventory movement. Some may also use them for a handful of other use cases, such as barcoding on shelves, documents, or expensive business assets.
On the other hand, manufacturers need to track all that and more. The manufacturing process generally has more moving parts than the average retailer. Manufacturers need to source a variety of different materials and components, keep track of what they use and don’t use, and track what stage of the process individual components are in. A barcode tracking system lets them keep track of that process in real-time.
In short, there’s a lot of moving pieces, and using barcodes makes it easier to track everything. Luckily, most inventory management systems include some sort of barcode functionality. So, chances are, even if you’re not using barcodes yet, you should be able to get started with them quickly enough. That’s assuming you’re using the right barcode manufacturing software.
Using a barcode system isn’t outright necessary, but lacking one can be crippling, as competitors will have a distinct advantage.
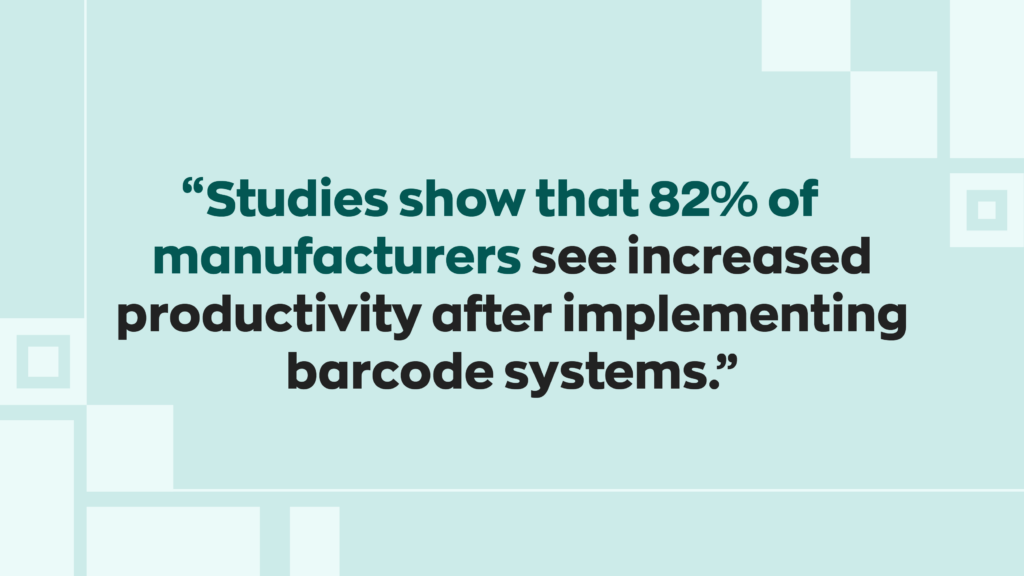
The benefits of barcodes for manufacturing
Manufacturers who utilize barcodes will see several benefits across their organization. Some of the major advantages are:
- Tracking stock levels – barcodes help monitor stock levels in real-time, making it easy to track raw materials, work-in-progress (WIP), and finished goods.
- Improved shipping and receiving – barcodes help streamline the pick-pack-and-ship workflow and make shipping and receiving fast and easy.
- Traceability – barcodes provide end-to-end traceability so you can easily track all your components as they travel through the manufacturing process.
- Equipment tracking – manufacturers can use barcodes to manage expensive equipment and machinery, ensure it’s always where it should be, and monitor its state of repair.
- Cost tracking – accurately tracking cost of goods manufactured (COGM) is among the most essential things a manufacturer can do, and barcodes make this process much simpler.
Do manufacturers need registered GS1 barcodes?
There are a few ways to get barcodes for manufacturing. The “official” way is to purchase them through GS1. They’re a non-profit business entity that seeks to connect places around the globe using the same barcode language. If manufacturers make their own unique product in-house, it’s a good idea to register it with an official GS1 barcode.
With that said, that doesn’t mean manufacturers need to use GS1 barcodes for the whole process. If anything, it’s a bad idea.
The reality is that GS1 barcodes are great for product authenticity and traceability and are a requirement if you want to sell your finished goods in major retail stores. However, there is no need to use them throughout the manufacturing process. You should reserve GS1 barcodes for finished products that are ready for sale.
So what about all the other barcodes you’ll need? You’ll be happy to hear you can make those barcodes in-house completely free! Here’s how.
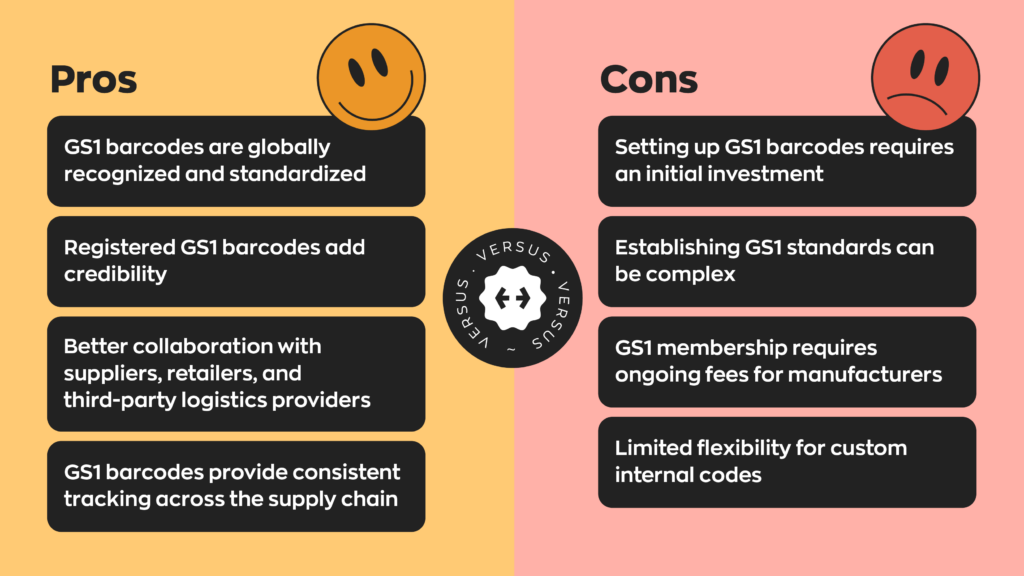
How do you create barcodes for manufacturing?
Unlike GS1 barcodes, when you create your own barcodes, they won’t be recognized by any outside organization. This means the only barcodes that matter to the outside world are the ones on your finished products. So feel free to create custom barcodes for all your components, assets, shelves, and anything else you want to track internally.
You have a few options to create barcodes for manufacturing:
- Barcode font – A barcode font isn’t much different from any other font you see in Word or Google Docs. Instead of changing the style of letters and numbers, a barcode font takes alphanumeric characters and translates them into barcodes.
- Barcode generator – A barcode generator is a tool used to generate barcodes in various barcode symbologies. Many free barcode generators are available online, each with varying functionality.
- Barcode manufacturing software – If you use barcode manufacturing software, chances are there may be a built-in barcode generator. For example, inFlow allows you to quickly generate barcodes of various symbologies with the click of a button. You can even create QR codes!
Where should you use barcodes?
The great thing about barcodes is just how versatile they can be. Manufacturers can use barcodes for many things, including barcoding components, shelves, documents, assets, finished products, etc. LPN barcodes, for example, are used by manufacturers to track the contents of large moveable bins.
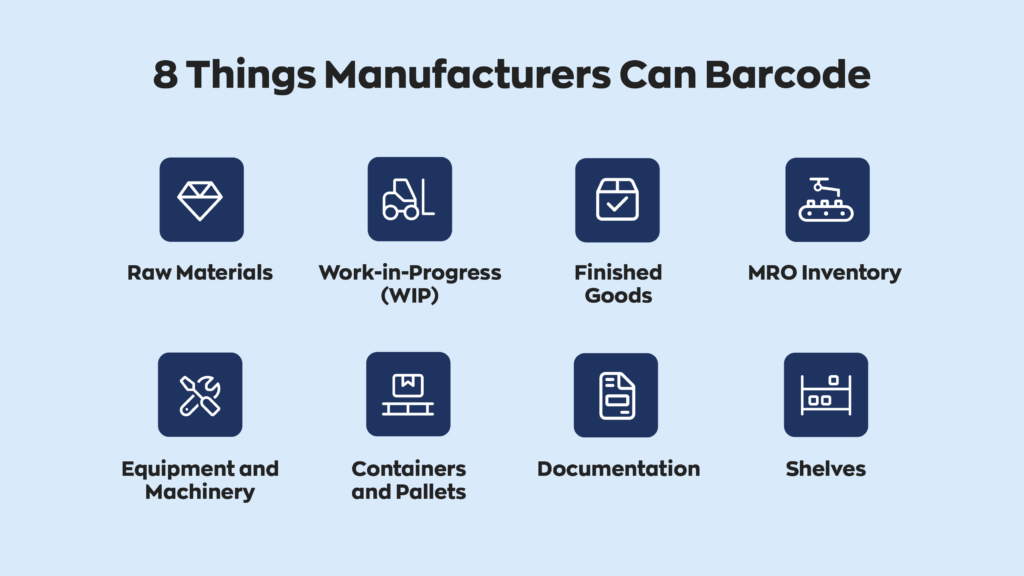
Manufacturers can use barcodes for their subassemblies and all of the components that go in a bill of materials (BOM). The bill of materials is a recipe that lists all the components that go into manufacturing a finished product. It’s a crucial tool for any manufacturer, and using barcodes to collect the necessary components for a BOM will increase speed and accuracy.
The possibilities are endless when it comes to barcodes for manufacturing!
What will you need to get started?
Using barcodes for manufacturing is essential for modern businesses, but the barcodes themselves are just one part of a system. You’ll need a few more things to get up and running. Every barcode system has four key components: barcodes, scanners, printers, and barcode manufacturing software.
In terms of a printer, any office jet printer will do if you’re looking for the cheapest option. Still, we recommend investing in a dedicated label printer for high-volume printing environments. For a scanner, you can get by using your smartphone if money is an issue. But if you’re scanning a lot, investing in a barcode scanner is best. There are many different options for both of these, so we recommend reading our articles on barcode scanners and printers to better understand which one would be right for you.
Wrapping up
While there are new technologies that seek to improve on barcodes, at the time of writing, they’re prohibitively expensive. Barcodes remain the primary method that manufacturers use to track their workflow and material/component levels. That won’t be changing anytime soon.
0 Comments