Key takeaways
- Construction material costs have experienced some volatility in 2025, mainly due to supply chain issues and global trade conflicts.
- Prices for copper, aluminum, and nickel remain elevated due to supply issues, raw material availability, and import costs.
- Both steel and lumber prices are expected to experience increased volatility in 2025 due to ongoing global trade conflicts.
- Contractors often struggle with budgeting due to the ever-changing cost of construction materials, which makes accurate estimates vital.
- To better manage material costs, you can build supplier relationships, use job costing, and adopt inventory software to track price changes and stock levels.
- inFlow helps businesses manage construction material costs by offering features like real-time inventory tracking, reporting features, and streamlined reordering.
If you’re a contractor, fluctuating building material prices are something you have to deal with regularly. There are a lot of things that affect construction material cost: inflation, demand, scarcity, supply chain issues, and so on. So: how do these factors affect building material prices? How do they affect your service price? And what are experts predicting for 2025?
What affects building material prices?
There are a lot of factors that affect construction material costs. Some are more relevant than others, and some have a more significant influence. Here are some of the major factors that affect construction material cost.
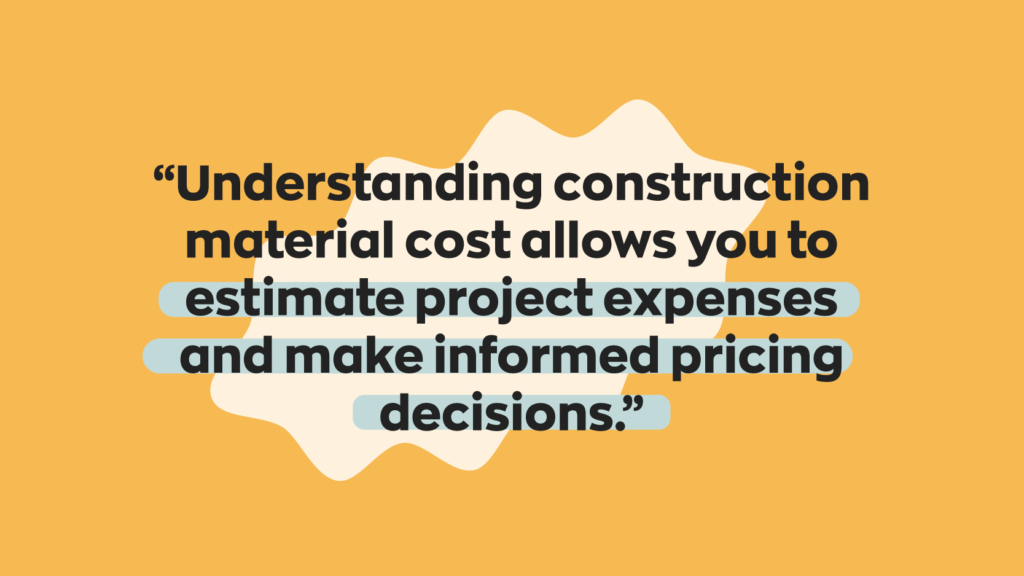
- Inflation is complicated. Really complicated. There are also a lot of factors that affect inflation, which means it’s extremely difficult to predict accurately. Government policy, spending, demand, and money supply are all volatile and affect inflation. As a good rule of thumb, the monetary value of materials will increase over time, but other factors may balance this out. While inflation has cooled toward the end of 2024, economists are worried about the impacts of recent developments in global trade relationships.
- Supply chain issues are straightforward, but they’re also an increasingly common issue. As the world continues to develop, supply lines become more and more congested. For example, the introduction of shipping containers changed the way that humanity transports goods around the globe. But there are only so many port cities, limiting port space. As the number of manufacturers continues to increase, so does demand, making supply chains more and more congested. There’s also the recent global trade war that has kicked off, putting further strain on the global supply chain.
- Unemployment may not be a direct part of material costs, but skilled labor is a resource. If not in active use, it leads to a variety of issues. It can lead to supply chain issues, making materials more scarce.
- Demand is part of economics 101, but it remains one of the biggest influences on construction material cost. The more demand for a material, the more people are willing to pay for it, driving costs up.
- Scarcity is another simple but influential factor. The less material there is, the more expensive it becomes, driving costs up. This is part of why supply chain issues are so significant. While difficulty obtaining a material doesn’t necessarily equate to scarcity, it has a similar effect.
How quickly does construction material cost change?
Construction is a fast-moving business, making this a difficult question to answer. There’s two big reasons for this. First, because there are so many influential factors, construction prices are extremely volatile, and construction material cost can change within the span of months or even weeks.
“Construction materials” is also a very broad term. It can refer to steel, copper, concrete, lumber, cement, oil, and so on. These industries all move at their own pace, resulting in different materials having different costs. They also have unique issues, ranging from supply chain issues to scarcity.
While these fluctuations tend to be incremental, there are instances where construction cost increases substantially. For example, during the COVID-19 pandemic and subsequent lockdown, the price of plywood nearly quadrupled, going from $400 to $1500 per square foot.
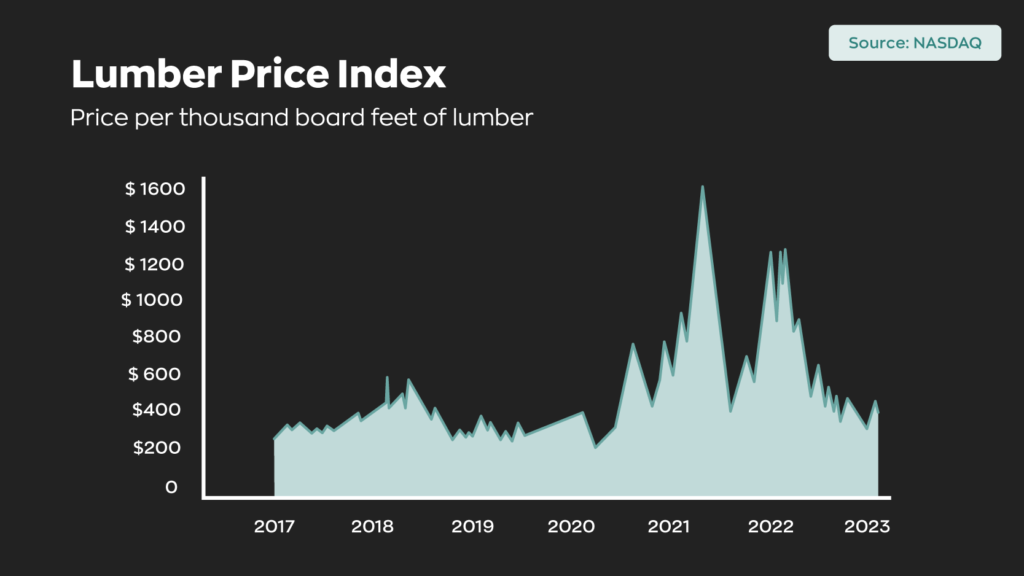
Keep in mind, though, that the pandemic was a global event that had an effect on every industry. The chance of another world-altering event like that happening anytime soon is slim but not zero.
What does the future look like?
Keep in mind that forecasting construction material cost changes is extremely difficult. It requires an excellent grasp of global market trends, an accurate demand forecast, and a lot of number-crunching. With that in mind, Linesight, a global consulting service, recently released its construction market insight reports based on geographic locations. Here are some of the key takeaways.
The demand for aluminum, copper, and nickel is expected to rise, driving up prices for electrical and construction work. This same demand could lead to equipment shortages. In particular, the scarcity of electrical steel leads to a lack of transformers, making equipment more expensive.
Prices for flat and stainless steel dropped significantly in 2024, though some volatility is expected in 2025 in the Americas due to new tariffs implemented by the Trump administration. These new policies could see the price of both steel and aluminum rising in the coming months.
Of particular note, lumber prices remained fairly stable in 2024 but have been experiencing some fluctuations. Some industry trends suggest that lumber prices may be influenced by both tariffs and housing demand. Which could mean a potential spike in prices very soon.
How does construction material cost affect you?
Generally speaking, if construction material costs increase, the price of construction services will increase. That’s the nature of doing construction: increase prices to maintain profitability. However, construction material cost is just one of the many factors that affect your service fees. Competition, profit margins, and market demand are a few other examples that influence service costs.
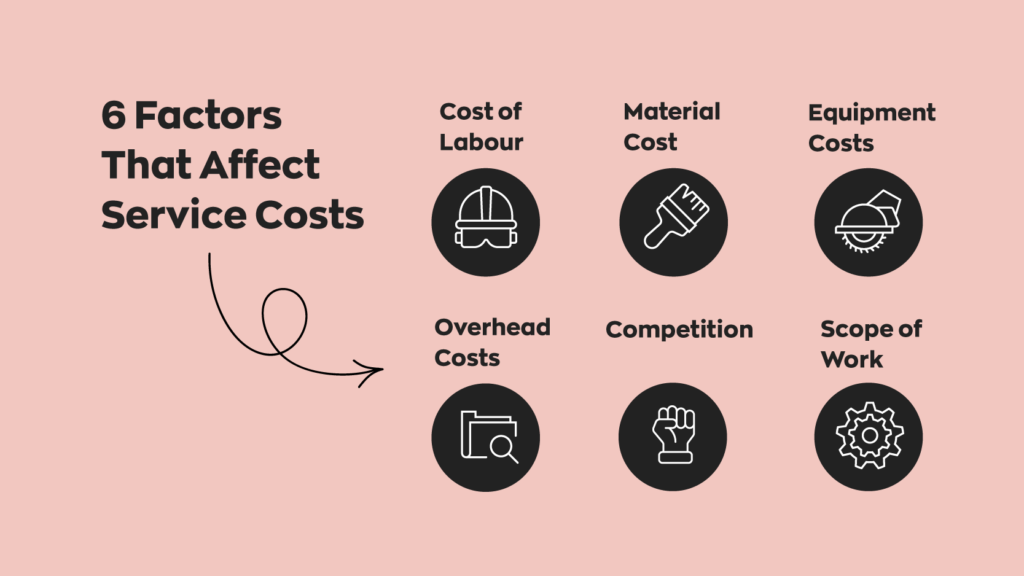
How should you keep track of material cost?
There are four popular inventory costing methods.
Average weighted cost may be the most popular costing method on this list. Using this method, businesses calculate their cost of inventory every time they make a purchase. To calculate the average weighted cost, divide the total cost of goods for sale by the number of units.
First-in, first-out (FIFO) is a method with which you use the cost of the oldest purchase to calculate the cost. For example, let’s pretend you buy a batch of 20 keyboards for $20 each. Later, you buy 20 more of the same keyboards for $15. Using FIFO, you would calculate the cost using a value of $20 since they were the first in.
Last-in, first-out (LIFO) is a bit of an oddball. The International Financial Reporting Standards (IFRS) has banned the use of LIFO, meaning that only US companies use it. Using LIFO, businesses calculate the cost of inventory using the value of the most recent purchase. To go back to the previous example, you’d calculate the cost of inventory using $15. Businesses in the US use LIFO because it reduces the amount they pay in taxes.
Manual costing refers to keeping track of inventory costs by manually assigning values to products. While this is the cheapest option in terms of monetary value, this method is generally unreliable.
Make use of field service management software
Another popular cost-saving method is using field service management software. Before the introduction of software, businesses would track material costs the old-fashioned way: lots of paperwork. On top of being tedious and inaccurate, it also created a lot of work, requiring meticulous record-keeping and frequent checks.
In the modern age, field management software like inFlow works in tandem with other applications you’re probably already using, like QuickBooks or Xero, keeping records accurate and updated in real time. With inFlow, you can track inventory levels, assets, and more. You’ll always know what was used, where it was used, and how much it cost.
Interesting article, thank you for sharing…
Hey Keshree,
Thanks for reading. If you enjoyed this article please consider subscribing to our newsletter below. You’ll get an email whenever we release new content.
Cheers,
Jared
Wonderful blog with quality information, thank you for sharing…
Hey NCL,
Thanks so much for reading. Please consider subscribing to our newsletter below to stay up to date with all our new content drops.
Cheers,
Jared
Interesting article, thank you for sharing…
Hey NCL,
Thanks so much for reading. Please consider subscribing to our newsletter below to stay up to date with all our new content drops.
Cheers,
Jared
Nice blog, thank you for sharing…
Hey Bison,
Thanks so much for reading. We’re glad you enjoyed it. Please consider subscribing to our newsletter below to stay up to date with all our new content drops.
Cheers,
Jared
Nice article, we appreciate your efforts. thanks.
Hey Nagarjuna,
Thanks so much for stopping by. We’re glad we could provide you with some useful insights. Please consider subscribing to our newsletter below to stay up to date with all our new content releases.
Cheers,
Jared
Very informative well done and concise
Hey Mike,
Thanks for reading! We’re glad you enjoyed the content. We aim to please 😉
Cheers,
Jared
Excellent overview of building materials in UAE! The construction industry here is booming, and quality materials are crucial.