Key takeaways
- Cycle time is the amount of time it takes a manufacturing process to convert raw materials into finished products.
- The cycle time formula is: cycle time = net production time / number of units produced.
- Cycle time is best understood alongside takt time (production rate to meet demand) and lead time (order placement to delivery).
- Understanding cycle time helps with resource allocation, planning, quality control, and cost management.
- Extremely low cycle times can sometimes impact the quality of your products.
In today’s world, many things depend on collecting relevant data. The manufacturing process is one of those things. For manufacturers to accurately measure the correct input and output of their products, they’ll need to understand their cycle times, and using the cycle time formula is an easy way for them to do this.
So, what are cycle times? How do you use the cycle time formula to calculate them? Why is knowing cycle time valuable for manufacturers?
Let’s jump into it, starting with the basics.
What is a cycle time?
When you boil it down, a manufacturer’s cycle time is the time that it takes for them to turn raw materials into a finished product. Keep in mind that in the world of manufacturing, “finished product” might mean different things from product to product.
For niche, highly customized products, a product could be finished but needs input from the customer to finalize the order. For example, if you’re a tailor selling custom suits, the product is only considered “finished” once your client tries it on and approves it. In these cases, the final cycle times can be more unpredictable.
How to use the cycle time formula
As important as it is, calculating cycle times is relatively simple. Just use the cycle time formula, also known as the timing formula. Here it is:
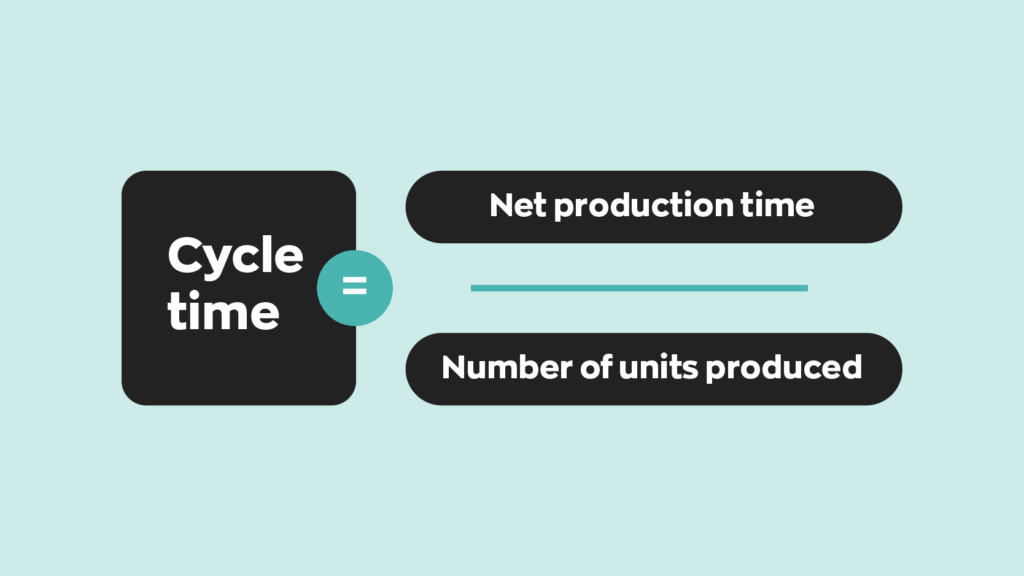
Net production time should account for any downtime in the manufacturing process throughout the day. For example, let’s say that a tile manufacturer takes 8 hours to make 200 tiles, but they experience 3 hours of downtime due to machine repairs. Their net production would be 5, and the number of units produced would be 200. Plugging those figures into the formula gives us this:
Cycle time = 5/200
You can take these numbers and whittle them down to 140, meaning that this imaginary tile company produces 40 tiles every hour. Let’s reduce this number further and figure out our cycle time in minutes. After all, in the world of manufacturing, every minute counts. Because one hour equals 60 minutes, we’ll set the “1” at the top to 60. That gives us this:
Cycle time = 60/40
Simplifying it further yields the following:
Cycle time = 1.5
That means the tile company produces one tile every one and a half minutes. It’s worth noting that we’ve chosen nice, clean numbers for this example, but it doesn’t always work like that. You’ll often find yourself with messy, uneven numbers.

So, now that you know what cycle time is and how to use the cycle time formula, let’s talk about why you should care.
Why is the cycle time formula important?
Now, as important as knowing the cycle time is, it’s still just a single data point. And a single data point is rarely ever useful on its own. It’s best to compare it to other data points or use it to gather more. Either way, it’s all about using (or gathering) more data.
In the case of the cycle time formula, an excellent place to start is to compare the results to other similar data points. There’s two data points in particular to be aware of alongside cycle time: takt time, and lead time. Here’s what you need to know about both of them.
Takt time
The term “takt time” comes from the German word “taktzeit”, which means “cycle time.” In the early 16th century, it was used to refer to regular rhythms, like that from a clock. In manufacturing, it represents the minimum production rate required to meet demand. Similar to the cycle time formula, there’s a formula used to calculate takt time.
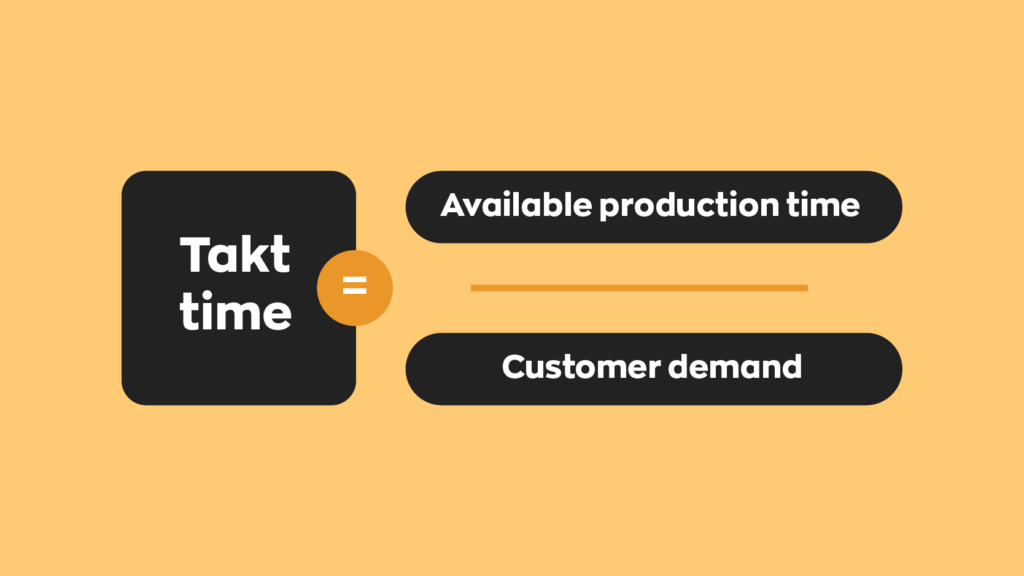
Let’s say that for a given month, the customer demand is 300 units. Sounds small, but big products require a lot of time. In that one month, let’s assume that there are 160 hours available for production. Setting up the equation looks like this:
Takt time = 160/300
That comes out to the following:
Takt time =0.53
This would mean the takt time is 0.53. This means that the business in question must produce 0.54 units per hour to meet the demand.
Manufacturing lead time
The term lead time can take on varying meanings depending on the industry. Lead time, in the manufacturing world, is the time it takes from when an order is placed until it’s delivered. Unlike cycle time, lead time considers everything from sourcing, preprocessing, and shipping. If the cycle time formula deals solely with the manufacturing process, then lead time takes peripheral processes into account.
The manufacturing lead time formula would look something like this:
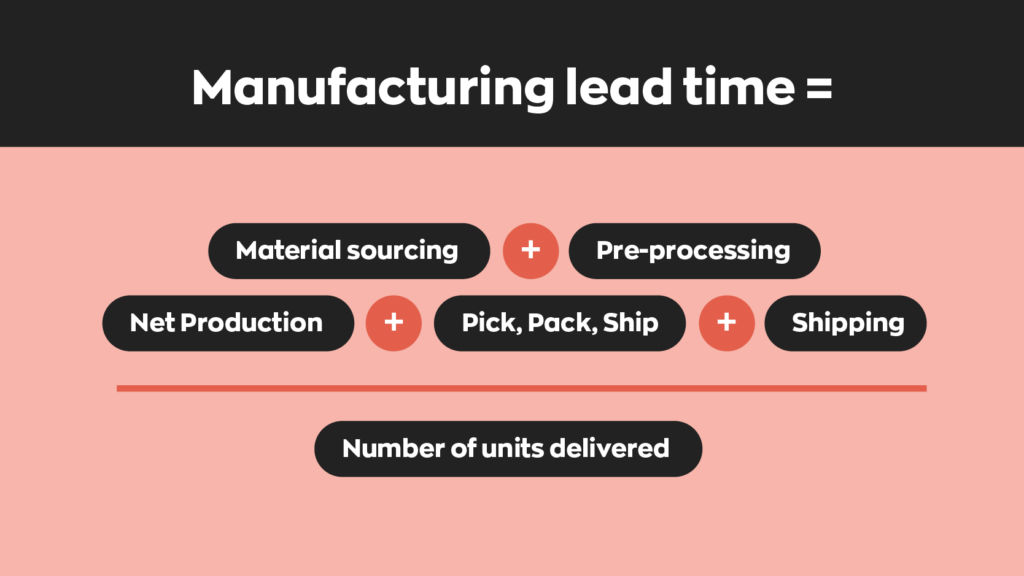
To help illustrate, let’s say your company fulfilled a shipment of 3000 units. It took 72 hours to source the materials from your supplier, 4 hours to prepare them for production, and 16 hours to manufacture them. Once finished, it took 2 hours to pick, pack, and ship them and 72 hours to reach their destination. Let’s put these numbers into the above formula:
Manufacturing lead time = 72h + 4h + 16h + 2h + 72h/3000 = 166h/3000 = 9960min/3000
That would mean that in this example, the manufacturing lead time would be 3.32 minutes per product.
What should you do with these data points?
Using some of these data points is pretty straightforward. For example, businesses use takt time to determine whether their output can meet demand. In the above examples, the cycle time is more than adequate to meet the takt time.
That means the output is capable of meeting demand. It’s not always as straightforward as comparing two numbers, however. Take manufacturing lead time, for example. On its own, lead time doesn’t tell you much. However, comparing it to cycle time can help identify inefficiencies.
For example, if the lead time is substantially higher than the cycle time– think three or more times greater– that’s a good indicator a business is spending too much time on peripheral tasks. This could include tasks like packaging, shipping, and managing supply lines. It could also indicate poor organization or other inefficiencies that cripple production.
Are lower cycle times always better?
In a word, no. Having a low cycle time is a good thing, but you need to ensure that those low numbers aren’t causing a reduction in quality.
Assuming that the demand exceeds the current production rate, you could (and should) find ways to reduce your cycle times. However, once you reach a certain point, reducing the cycle time too much can sometimes mean a drop in quality or an increase in errors. When you’ve reached this point, it’s best to consider scaling your operation rather than reducing your product cycle time.
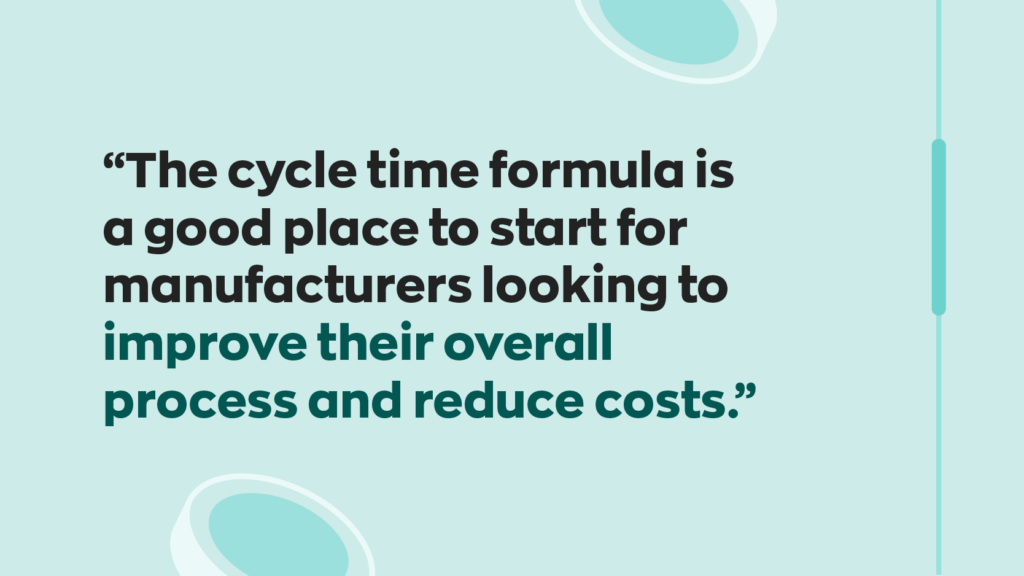
And as with anything, there’s a balance between quantity and quality. If you don’t meet that balance, you’ll find your customers leaning towards your competitors.
Don’t count on the cycle time formula alone
As helpful as the cycle count formula is, it only yields a single data point. And on its own, there’s only one thing that it tells you. Similar data points like takt time and manufacturing lead time can yield more information when used in conjunction.
Harnessing the power of manufacturing software, like inFlow, can be especially useful when collecting valuable information about the manufacturing process. Our customers love the reporting features we’ve included in our system that make finding valuable data points quick and easy. We’ve also tailored our software better to fit the needs of manufacturers, big and small. Our most recent manufacturing update includes features like kitting/bundling and manufacturing orders (MOs).
Not to mention the robust barcode system built right into our software. With the added speed of barcodes, manufacturers can reduce their cycle times significantly. You can scan barcodes to receive your shipments of raw materials and use them to pick and ship your orders right inside inFlow!
0 Comments