The heating, ventilation, and air conditioning (HVAC) industry is really complex when it comes to tracking inventory. HVAC technicians are dispersed across various job sites, each with unique inventory needs, and the absence of even a single component can bring an entire job to a screeching halt. This is why HVAC inventory management isn’t just beneficial; it’s crucial.
But even with so much at stake, you would be amazed by how many HVAC businesses let their inventory management take a backseat. So, for today’s topic, we’ll dive into the ins and outs of HVAC inventory management.
Think of this article as a roadmap for new and seasoned HVAC companies to get their inventory in check. We’ll help you understand the importance of managing your inventory, how to identify problems and provide actionable tips on how to improve your workflow.
Understanding the importance of HVAC inventory management
Experts expect the HVAC industry to see continuous growth through all of 2024 and as far as 2030. This makes the HVAC market both lucrative and consistent— a bit of a rarity in today’s world of frenetic capitalism. But with growth comes more complications. You’ll have more things to manage and maintain, including employees, customers, warehouse space, and inventory.
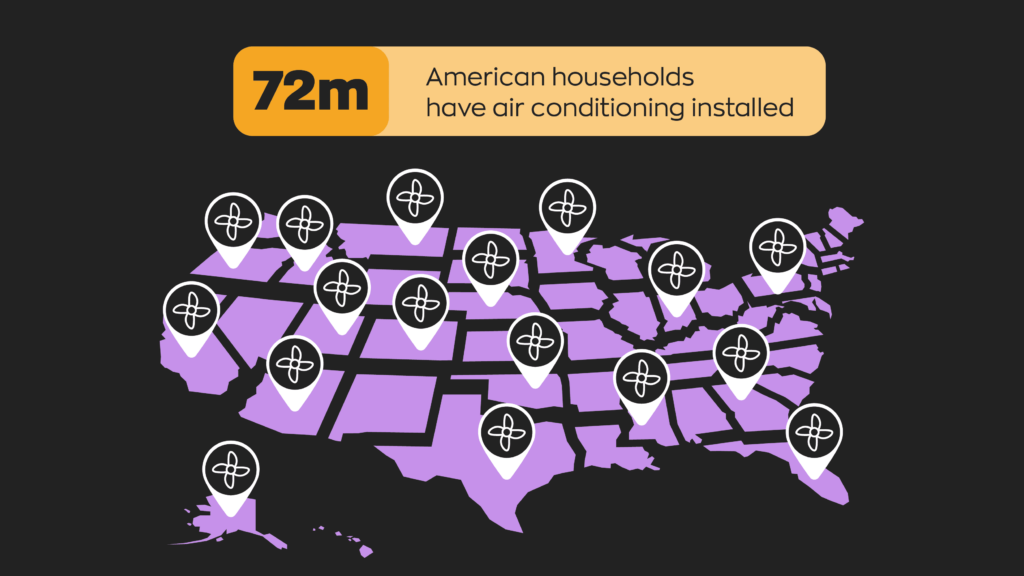
As your HVAC business grows, you’ll quickly feel the strain if you still manage your inventory via spreadsheets or pen and paper. You’ll have less visibility overall and be much more vulnerable to things like stockouts. By practicing good HVAC inventory management, you’ll ensure your technicians always have the required parts when needed. This will prevent costly delays and result in a more satisfied customer base.
Symptoms of poor HVAC inventory management
Although they work in the same industry and adhere to the same standards, different HVAC companies often specialize in different things. For example, one may specialize in residential HVAC systems, while another may specialize in commercial ones.
Despite these differences, they all tend to run into similar issues. Here are some of the most common downfalls of suboptimal HVAC inventory management.
Negligent tracking
Something that you, as an HVAC business owner, always have to be aware of is where your components and materials are. This also applies to your equipment and tools. HVAC technicians regularly use heavy equipment, and some of the materials they work with can be dangerous. For example, if AC coolant leaks, it can cause respiratory issues and mild chemical burns.
Negligent HVAC inventory management has other ramifications as well. We’ve mentioned this earlier, but it bears repeating. HVAC systems are built out of many different parts, and all of them are important. In extreme cases, forgetting just one part might mean starting over, which causes a considerable revenue loss. In less extreme cases, dispatching a technician without a necessary tool means they have to return. That pushes the whole schedule back, often resulting in an angry customer.
All of the above is made more difficult by the fact that each technician has different needs. Different jobs require different tools, and part of field service is figuring out the most efficient routes. You can think of it like a jigsaw puzzle. Figuring out where every piece fits is key. HVAC inventory management software can help solve this.
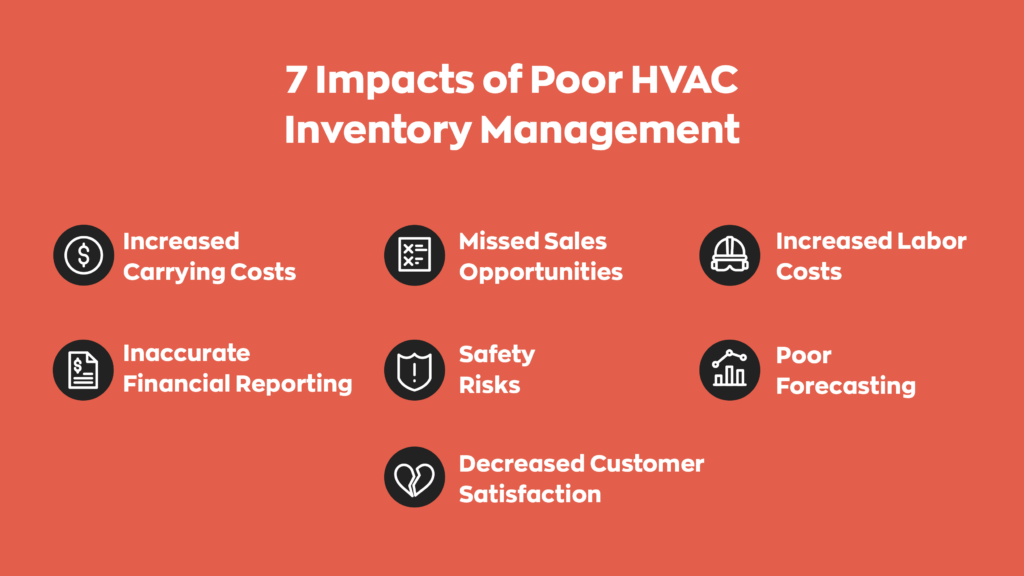
Poor forecasting
Demand forecasting can be tricky for HVAC businesses. The parts they use are very diverse and have varying usage rates. There is also seasonality to consider. It’s common to experience an influx in business during hot or cold weather due to more people using their HVAC systems.
Proper demand forecasting involves analyzing data to accurately predict your business’s needs. Without HVAC inventory management software, collecting the necessary data will be much more challenging.
Understocking and overstocking
No matter your industry, the key to good inventory management is finding the perfect balance in your inventory levels. Carrying excess inventory will eat away at your profit margins, and understocking might mean missed shipments.
In HVAC inventory management specifically, understocking is arguably more damaging than any other sector. Not having enough inventory slows down job completion, hindering overall revenue. Overstocking, on the other hand, means you’re tying up capital somewhere you don’t need it.
To solve this issue, you’ll need to identify your ideal inventory levels. However, to determine that magic number, you’ll need in-depth knowledge of both your business and the surrounding market. This ideal level is also subject to short-term changes as market demand fluctuates.
Inefficient workflow
When you run an HVAC business, you’re going to have various technicians on job sites all over the place. These technicians have a lot to juggle, like customer service, diagnostics, repair, and logging used components. If your workflow involves updating spreadsheets or physical inventory records, it’s only a matter of time before things get out of control.
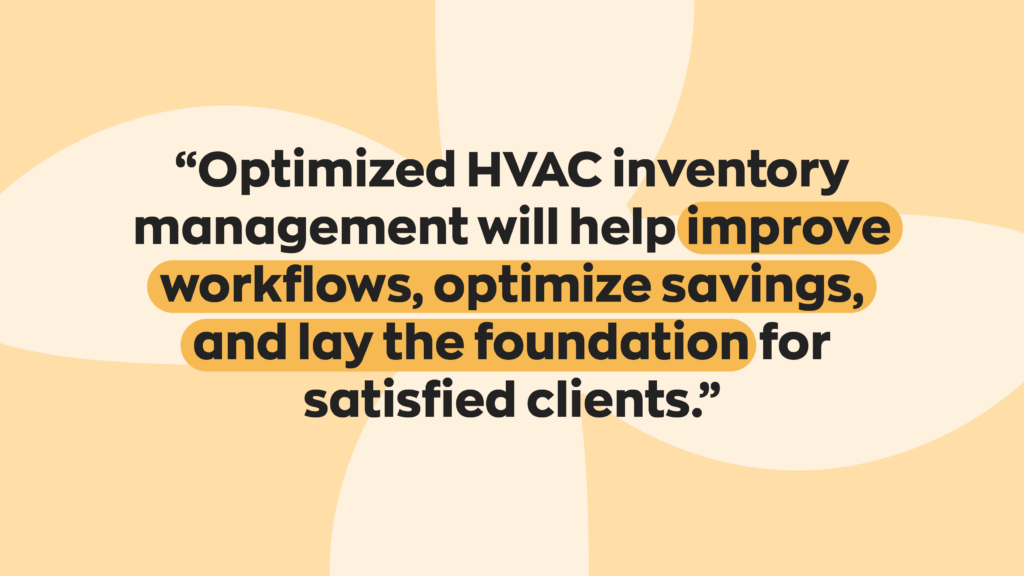
This type of workflow will inevitably result in severe mistakes, such as inventory shortages and lost assets. You’ll also need to conduct more frequent inventory audits, requiring more wasted resources.
What can you do to avoid these issues?
Although occasional problems are inevitable, there are ways to minimize them. Here are some best practices for HVAC inventory management to help:
- Conduct regular cycle counts—Even if you use HVAC management software, you’ll still need to conduct counts. This is extremely important for field service, as equipment and materials are always on the move. Something’s bound to slip through the cracks somewhere.
- Set strict reorder points—Many of the components and equipment HVAC technicians use are expensive. Even a moderate overstock could eat up a lot of capital. Keeping your inventory low also minimizes the physical space you need.
- Adopt a mobile job site workflow—This type of workflow has become increasingly common in the field service industry. It involves treating each technician’s truck as a separate location and using your main warehouse to transfer stock to your trucks when they need to be replenished.
- Analyze historical data—You can’t predict the future, but you can get a pretty good idea of what it’ll look like. Collecting data regarding inventory movement across a period of time can help decide how much to stock. It can also offer insight into areas for expansion.
- Use HVAC management software—What’s great about HVAC software is that it makes implementing all the above points easier. Our field service management software, inFlow, makes cycle counts a breeze and allows you to set reorder points. You can set up multiple locations, allowing you to adopt a mobile job site workflow seamlessly. Our reporting features will help you analyze your data, and we have a built-in barcoding system to make scanning your products in and out faster and easier.
Interested to learn more about mobile job site workflow? Watch our video below!
Use the right tools for your HVAC inventory management
Managing inventory for HVAC is naturally complex, but using the right tools makes things a lot easier. Thankfully, in the modern day, there’s software to make HVAC inventory management easier and more manageable.
Adopting these tools early on will set you up for success. You’ll be much more prepared for growth and increase your chances of success. So give inFlow a try today to give yourself a competitive advantage!
0 Comments