Key takeaways
- The make-to-order (MTO) manufacturing process involves producing products only once an order is placed.
- In contrast, make-to-stock (MTS) production is done in bulk based on demand forecasts to ensure availability.
- MTO allows customization, minimizes waste, and reduces storage needs, but it also has longer lead times, higher costs, and complex order management.
- MTS leads to lower production costs, bulk purchasing advantages, and faster fulfillment, but it requires accurate forecasting to avoid excess inventory and storage constraints.
- Make-to-order is ideal for high-cost, customizable, or perishable products, whereas MTS suits mass-market items with steady demand.
- Success with MTO relies on understanding customer needs and closely monitoring production quality.
- Make-to-stock businesses rely on accurate demand forecasting, leveraging economies of scale.
- Regardless of your manufacturing process, every business can benefit from manufacturing software to better track its workflow.
If you work in manufacturing or assembly, choosing the proper manufacturing process can be the difference between profitability and operating at a loss. This is because not every manufacturing process is suitable for every product. For example, a business that sells custom furniture will undoubtedly have a different process than a company that manufactures cell phones. For this reason, there are several different manufacturing processes, each with its own unique use case.
Today, we’ll focus on two distinct manufacturing processes: make-to-stock (MTS) and make-to-order (MTO). We’ll discuss the differences between the two, offer advice on which might be suitable for your products, and review some best practices to help you get started.
What is make-to-order (MTO)?
For the most part, make-to-order is precisely what it sounds like. Instead of producing in bulk, businesses manufacture their orders as they come in. This approach allows companies to tailor their products to their customer needs. It also dramatically reduces the risk of overproduction.
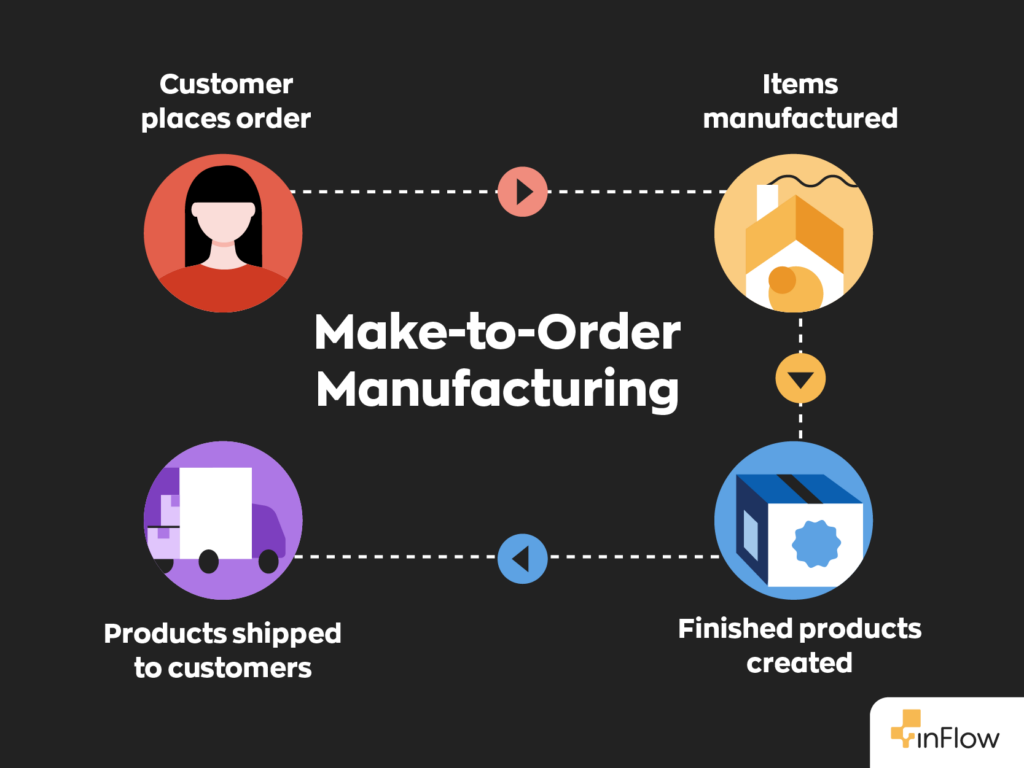
Benefits of make-to-order
As with any business model, make-to-order has both benefits and downsides. Here are some of the benefits of make-to-order:
- Reduced Storage Demands—make-to-order manufacturing only occurs when you receive an order, so you don’t need to store as many raw materials. Additionally, since every product you produce has already been sold, there is little need to store finished goods.
- Less Waste—demand-driven production minimizes the risk of your products becoming obsolete, lost, or even stolen.
- Customization & Personalization—low-volume production runs allow you to customize your products according to your customers’ needs.
- Adaptability—make-to-order will make your business much more agile. You’ll be able to pivot more quickly to meet shifting customer demands.
Drawbacks of make-to-order
As always, some downsides come along with make-to-order production. Here are some of the biggest ones to consider:
- Longer Lead Times—producing products only when an order comes in means it will take longer for your customers to receive the product they ordered. In today’s world of Amazon’s same-day delivery, this could prove problematic.
- Higher Production Costs—small batch production can lead to higher per-unit costs compared to mass production.
- Complex Order Management—as we mentioned earlier, make-to-order products tend to be more customizable, which makes managing these orders much more difficult.
- Limited Scalability—small production runs and highly personalized products mean scalability will be near impossible without a substantial investment.
What products are best for MTO?
As a good rule of thumb, expensive products designed to be customizable are suitable for make-to-order manufacturing. Examples include custom computers or furniture with various potential configurations.
However, many other products would benefit from an MTO production strategy—for example, perishable items such as food and pharmaceuticals. Take a chocolate manufacturer, for instance. The freshness of their products is paramount, so mass production without orders to fill may not be the best idea since the quality of their chocolate will diminish over time.
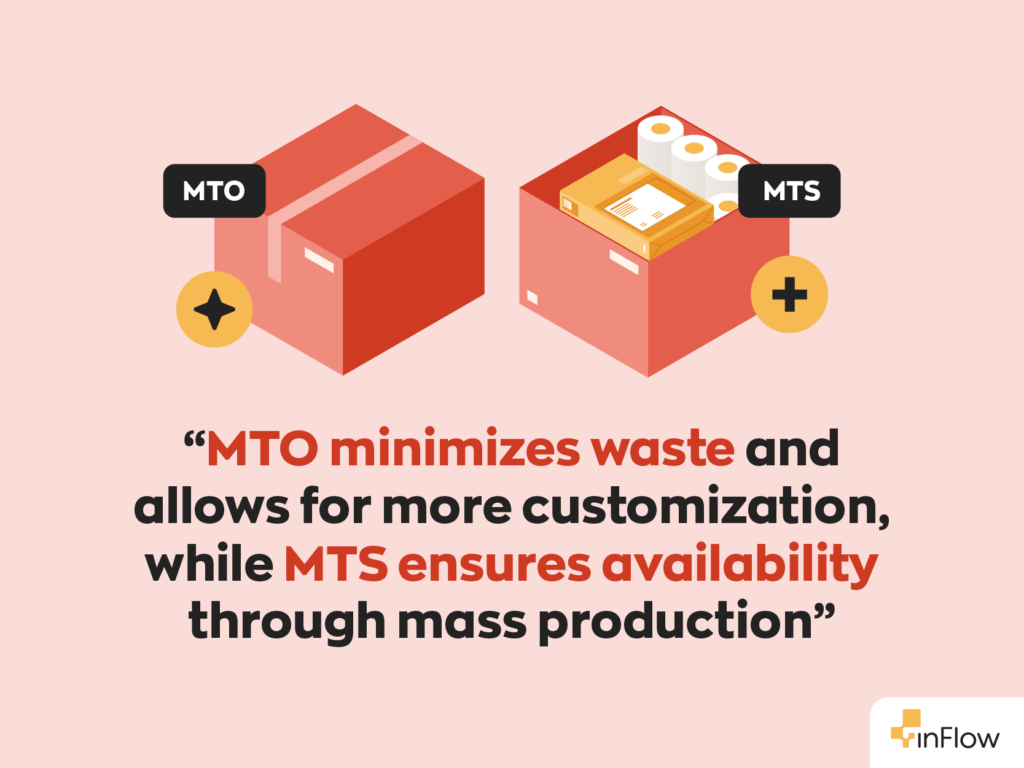
MTO best practices
Knowing what MTO is and how to implement it are two different things. Here’s some best practices to help you bridge that gap.
Understand your customer’s needs
As we said above, make-to-order tends to favor expensive, customizable products. Understanding what your customers need and how to provide that with your product is key. For instance, let’s look at a company that provides components for data centers. While all data centers generally function similarly, the racks, cooling solutions, and drives required may differ according to needs.
Keep a close watch on your manufacturing process
Quality products are essential, and that goes doubly so for custom ones. Customers who pay a premium to get exactly what they’re looking for demand a certain level of quality. This is why it’s vital to monitor your manufacturing process closely. The best way to do this is to use manufacturing software.
It’ll track things as they move through the manufacturing process, ensuring quality and timely delivery. Systems with barcodes are another excellent boon and help track every individual component throughout the manufacturing process.
Consider adopting lean manufacturing
We’ve discussed lean manufacturing before, so we won’t go too in-depth. To summarize, lean manufacturing is a process that aims to streamline and optimize every stage of manufacturing. It can help reduce waste, defects, and operating costs if done correctly.
What is make-to-stock (MTS)?
When someone hears “manufacturing, ” make-to-stock (MTS) is probably the first thing that comes to mind. Rather than manufacturing products as orders come in, make-to-stock manufacturers produce large batches all at once and store them for future demand. This production strategy relies heavily on demand forecasting to determine optimal stock levels.
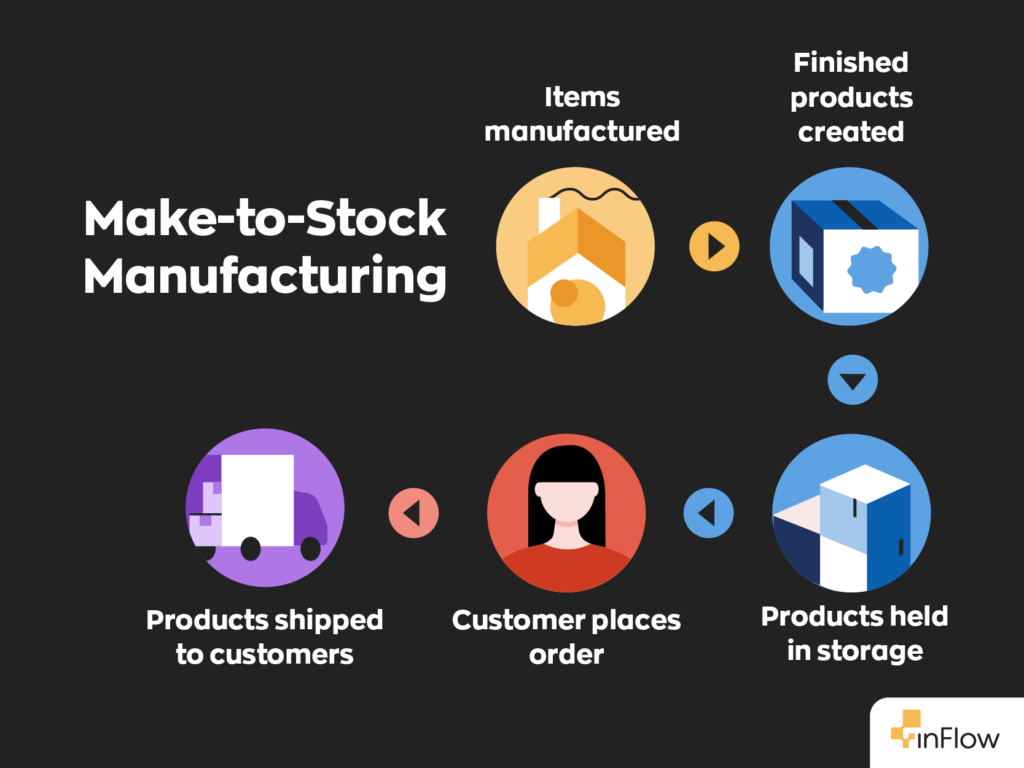
Benefits of make-to-stock
The make-to-stock production strategy has been widely adopted in the manufacturing industry because of its vast array of benefits. Some of these benefits include:
- Shorter Lead Times—producing products en masse means you’ll have plenty of inventory ready when an order comes in, expediting your order fulfillment process.
- Lower Production Costs—mass production runs lower production costs through economies of scale. The result is a lower cost per unit.
- Bulk Purchasing Advantages—when you manufacture large quantities of products simultaneously, you’ll need a lot more raw materials, and businesses can negotiate better prices with suppliers on high-volume purchases.
- Increased Sales Volume—the ability to produce more inventory means you can sell at a much higher volume.
Drawbacks of make-to-stock
The make-to-stock production strategy isn’t perfect and comes with several downsides. Some of those include:
- Storage Space Constraints—if you use the MTS production strategy, you’ll need large amounts of raw materials ready at a moment’s notice. Not to mention, if you’re creating products in bulk, you’ll need to store your finished goods until they are sold.
- More Waste—with high levels of stock to manage, there is a greater chance that things may become obsolete, damaged, lost, or stolen. Even a small mistake in forecasts may result in a ton of excess inventory.
- Limited Customization—make-to-stock relies on manufacturing products beforehand. This production strategy leaves little room for customization, so making changes based on customer preferences will be difficult.
- Slow Response to Market Changes—if your business operates with an MTO production strategy, you might find it hard to adjust production or pricing if there is a sudden shift in customer sentiment.
What products are best for MTS?
Because of its batch production methodology, make-to-stock is suitable for products with a consistent demand. For example, consumer electronics, small toys, and everyday household items.
For instance, a business that manufactures silicon kitchen utensils can confidently mass-produce spatulas since every customer wants the same thing. Something simple that serves a specific function.
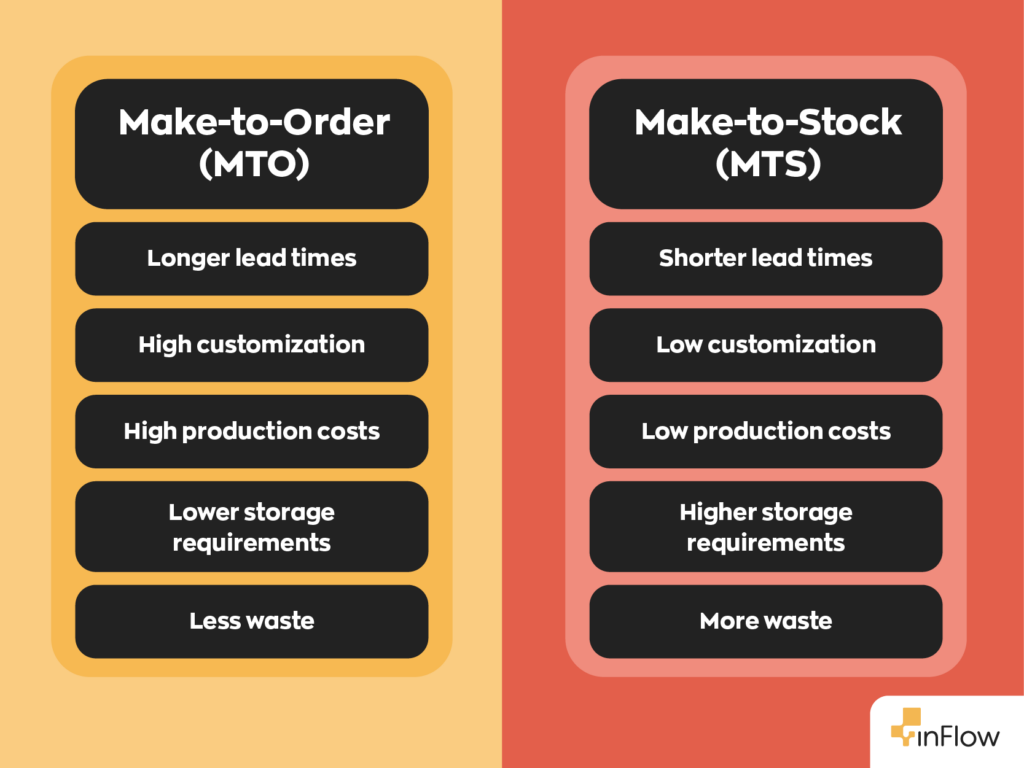
Best practices for make-to-stock
While MTO may be the most “traditional” manufacturing process, implementing it efficiently isn’t easy. Here are some best practices to help you get started.
Invest in accurate forecasting
Accurate forecasting is crucial for any make-to-stock business. It ensures that you maximize profits, all while reducing risk and avoiding over or understocking. If there’s one takeaway from this segment, it should be this one.
Take advantage of economies of scale wherever possible
Economies of scale refer to the fact that, typically, manufacturing larger batches drives down the per-unit price. This is a massive benefit to manufacturers who can take advantage of it. It reduces operating costs and also results in a higher per-sale profit. However, doing so carries some risks and depends on accurate forecasting.
Track your manufacturing process
Whether your manufacturing process is make-to-order, make-to-stock, or assemble-to-order, tracking your production process is key. This is why all manufacturers can benefit from manufacturing software. It’ll help keep close tabs on every stage of the process.
Wrapping up
Choosing between make-to-order, make-to-stock, or any other manufacturing process depends on various factors, including product type, demand, and storage capabilities. While MTO can reduce carrying costs and waste, it requires incredibly efficient order processing and production scheduling.
On the other hand, MTS ensures your business always has products ready to meet demand, but your overhead costs will suffer. You also run the risk of overproduction and being left with deadstock.
It’s essential to weigh all your options before deciding which production strategy suits you.
0 Comments