Your warehouse’s fulfillment process can be complex, but it doesn’t have to be! By setting up sublocations in a certain way you can optimize your sales order fulfillment, saving you and your team time and headache!
The best layout for warehouse optimization
There are several ways to lay out your warehouse based on your needs, but we recommend an industry best practice that organizes aisles like streets, as shown in the picture below. With this style, each aisle is denoted with a marker (in this example it’s A, B, C, D, etc.).
Then each section within that aisle is denoted with a dash and a new marker (in this example it’s 001-010). This results in each side of your aisle being either all odd numbered or even numbered—just like a typical street numbering system used in North America.
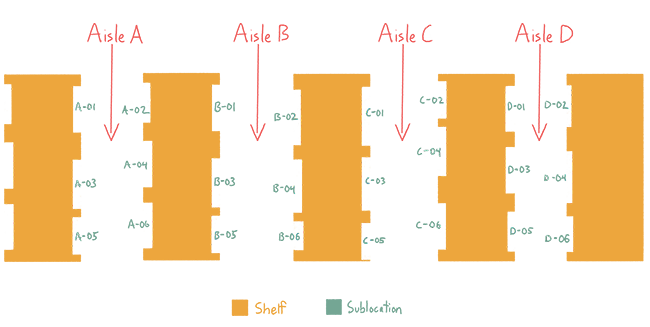
My warehouse is a bit more complex — how do I account for multiple shelving units?
Of course, within each section of the aisle there may be multiple storage units (e.g. multiple levels of shelves or bins). Simply add a new marker to your numbering convention, separated with a dash.
For example your sublocation could be A-06-C (Aisle A, Shelf 06, Bin C).
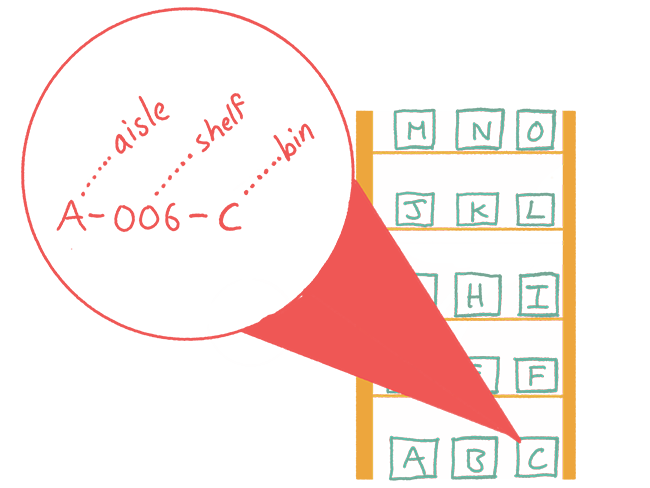
Each format can be customized to fit your warehouse. For example, if you have many small bins within a section, try using a digit instead of a letter for your sublocation (e.g. A-06-037 instead of A-06-AK).
Why optimizing your warehouse route improves order fulfillment rates
This convention works for most warehouses as it helps you understand where products are at a glance:
- Aisle: Roughly how deep into the warehouse a product is located.
- Section: Roughly how far along the aisle a product is located, and which side of the aisle it’s on (based on if it’s an odd or even number)
- Bin: Roughly where on the shelf a product is located (e.g., Bin A might be at ground level, while Bin L might be high up enough that it requires a ladder to get).
This method saves you time and headaches — no more running laps around the warehouse. Now you can hit the warehouse floor with a simple picking plan that navigates you in a straightforward, efficient way!
To get the most use out of this optimized system, it’s important to remember these general rules:
- Store products in one primary sublocation.
- Store only one type of product in each bin.
- Put most used items in the most accessible spots (i.e. lower on the shelves).
- Create overflow locations to account for excess inventory – this is usually on top of shelves or a dedicated overflow section of the warehouse where overstock products live.
How to physically label your warehouse
The recommended way to set up your warehouse labelling system is as follows:
- Aisle: Large, highly visible signs on the ends of your aisle (Aisle sign example)
- Section: Medium, visible signs, typically sticking out of shelves (Section sign example)
- Bins/Shelves/etc.: Smaller labels with barcode (Bin label example)
To print labels for your warehouse we recommend printing from inFlow using a DYMO label printer.
Sticking labels can be messy and hard to remove afterwards. We recommend the following options for a cleaner, easier way:
- Corrugated bins: Get corrugated cardboard bins, like these ones: https://www.uline.com/BL_311/Warehouse-Rack-Bins. Stick the labels onto the bins instead of the shelves themselves. Corrugated bins are inexpensive and a great way to organize products!
- Magnets (if you have metallic shelves): You can create magnetic labels that are easy to stick onto and remove from metallic shelves, like these ones: https://www.uline.com/BL_1225/Magnetic-Warehouse-Labels-Perforated-Rolls<
- Removable labels: Get customized barcode labels that are designed to look good and can be easily moved. Feeling fancy? check out ID Label
How inFlow optimizes your warehouse fulfillment process
Great news — inFlow Inventory supports the street style numbering system explained above!
That means that when you set up sublocations in inFlow using the suggested naming conventions, inFlow will recommend an optimized picking route so you can hit the warehouse floor with an efficient plan of attack!
To see this in action, when you create a customer order simply navigate to the Pick tab and select Auto Fill. The items will populate based on the ideal picking order according to your sublocations, as seen in the example below.
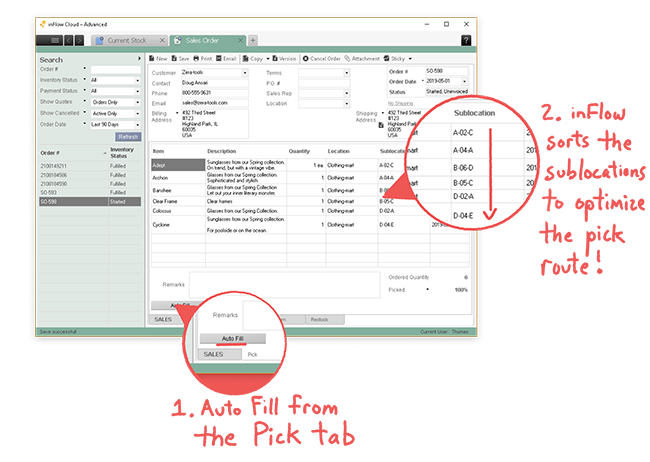
To demonstrate, the image below shows you inFlow’s recommended picking route when you apply the street style numbering system. The six stops are made in an optimized way that only require passing through each aisle once.
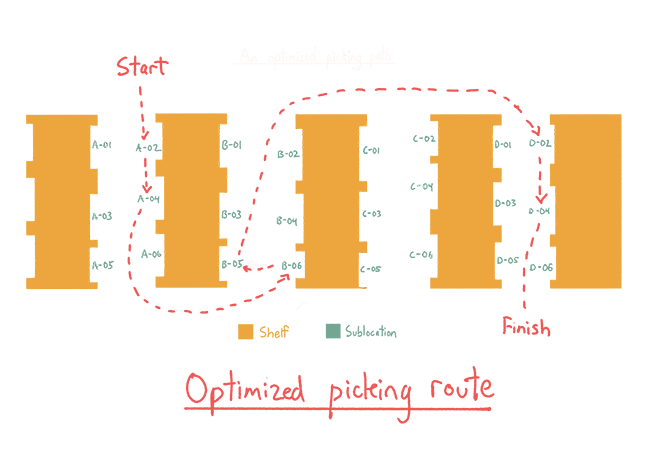
As a reminder, when you set up sublocations in inFlow using the recommended system above, remember these guidelines:
- Separate Aisles, Sections and Bins/Shelves with a dash (e.g. correct: A-06-C, incorrect: A06C).
- Use a leading zero when using numbers — this make sure your inFlow reports are sorted correctly (e.g. correct: 06, incorrect: 6).
What if I don’t need to follow the street style numbering and picking system?
inFlow is automatically set up to support street style numbering and picking system for your fulfillment process. It is a built in feature that can’t be turned off at this time. If you don’t follow this naming and warehouse convention – no problem! This built in feature won’t negatively affect your workflow, it’s just an added bonus for those who do follow the street style system.
Have a different way of organizing your warehouse? We’d love to hear about it in the comments!
Will you be implementing Street Style Routing into the on-premise version. We are still using On-Premise (V3.6.1) and have developed integrations at the SQL database level for our website and are not ready to move to the cloud version.
Hi John, thanks for stopping by!
I’m sorry, we are no longer adding new features to inFlow On-Premise. We’re making sure that On-Premise continues to work and we provide technical support with the Support Plan, but we’re focusing our development time on Cloud.
I’m sorry that inFlow Cloud isn’t a good solution for your business at this time. I usually try to suggest a workaround, but for your use case with custom SQL, I agree that On-Premise is the best solution for right now. I’ve taken your feedback and I’ll make sure to pass it to our product team for review.
Awesome work.Just wished to drop a comment and say i’m new your journal and adore what i’m reading.Thanks for the share
Can inflow integrate with Microsoft dinamics F and O?
Hey Adrian,
Thanks for stopping by! To answer your question, no inFlow does not natively integrate with Microsoft Dynamics F and O, however, it may be possible through the API. I hope this helps 🙂
Cheers,
Jared
HI, are You planning to add a signature validation for the mobile app, when the customer picks up the order?
Hi Raul,
Thanks for getting in touch about this! I’m sorry but at the moment inFlow isn’t capable of signature validation for the mobile app. It’s certainly an interesting suggestion but presently it’s not possible in this system. We’ve gone ahead and logged this feedback with our product team to see if we can add this feature in the future.
Cheers,
Jared