A business runs on currencies. Not just fiat currencies like USD, CAD, or the Euro, but abstract currencies as well. Things like time, opportunity, and so on. Because of this constant resource drain, businesses are always looking for ways to increase the efficiency of their day-to-day operations. Manufacturing is no different: the more efficient your processes, the more profitable the business. One product of this race for efficiency is the distinction between push vs pull manufacturing. So: what is a pull system? A push system? What is push vs pull in supply chain systems? Which one should you be using?
What is a push vs pull system?
Think of the way you breathe. When you breathe in, all the air you pull in ends up at the same spot. In that sense, it’s more focused. When you push that air out of your lungs, it becomes scattered everywhere. Push vs pull manufacturing follows a similar concept.
- Pull manufacturing is a form of just-in-time (JIT) inventory management/manufacturing. Instead of keeping the shelves stocked at all times with many different products, businesses purchase components as orders come in. This makes the pull system a more focused and cost-effective inventory method of manufacturing.
- Push manufacturing is when manufacturers create as many products as possible at any given time. This method relies heavily on sales forecasts and could result in unsold products. Unsold products are not only a direct loss in capital but have an overhead cost as well. For this reason, push system manufacturing comes with a much higher financial risk.
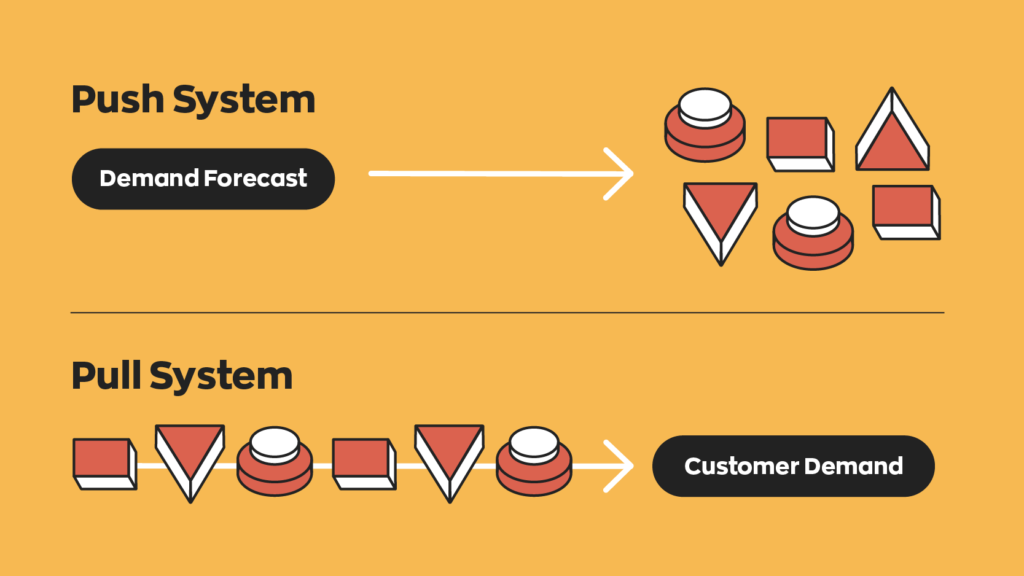
When to choose a push vs pull system?
Before getting into the nitty-gritty, it’s essential to understand that neither of these systems are a one-size-fits-all kind of thing. Pull manufacturing generally allows for greater control, while push manufacturing is the “safer” of the two. A good rule of thumb is that products with high individual value (that is, cost per unit) benefit from pull manufacturing. Conversely, products with low individual unit value work best under a push system.
What are the benefits of pull system manufacturing?
Like any financial or business system, push vs pull systems have benefits and drawbacks. If we focus on the details, we’ll be here all day (and who has time for that?), so we’ll focus on the important ones.
Pull manufacturing emphasizes control above all else. Instead of buying components in bulk, they’re purchased only when needed. This results in a few things.
First, pull manufacturing leads to a smaller inventory. This means that there’s less capital tied up in the warehouse. Because there’s also less inventory to handle, it makes keeping track of things much more manageable. And the more time you save tracking inventory, the more money you save.
Remember, though, that JIT inventory management comes with its own risks. Buying components as you go means you’ll lack the “safety net” of extra inventory. A slight miscalculation could result in missed shipments or product backorders, inevitably pushing your customers toward competitors.
What are the benefits of push system manufacturing?
On the other hand, push manufacturing trades control for ease of access and shorter travel times. This makes sending or receiving inventory easier because it’s all in bulk. It also means that there’s no wait time between order and delivery. Since you manufacture products ahead of time, you can fulfill customer orders the day you receive them.
Manufacturing in bulk leads to its own issues, however. These issues stem from how the process relies on sales forecasts. While sales forecasts can be incredibly accurate, there is always an inherent risk of being left with unsold inventory. Not only does stored inventory increase your carrying costs it also runs the risk of becoming dead stock, which would result in a direct loss of capital.
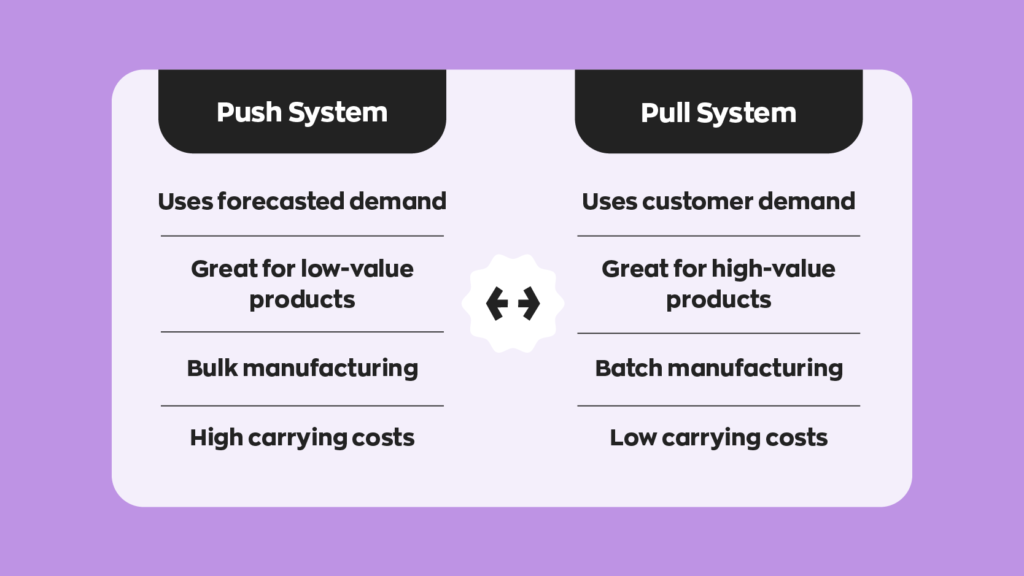
Pull vs push system: which should you use?
The are various factors that feed into the pull vs push system debate. Ultimately, we can’t point at your business and tell you what you should or shouldn’t do. What we can do is give you a few pointers and explain some best practices. Here are some things to consider if you’re trying to decide between a push vs pull system.
Consider the cost of a single unit of your product. Because a pull system involves manufacturing in bulk, the higher the cost, the higher the risk. Manufacturing one-by-one as orders come in lowers that risk, primarily if you deal with more expensive products.
A good example is a car dealership vs a grocery store. Because a car is significantly more expensive than food products, there’s a more significant potential for loss. For this reason, it would be wise to manufacture cars based on a pull system and only manufacture them as needed. This helps reduce risk and keeps costs relatively low. The Toyota Production System (TPS) is closely based on this philosophy.
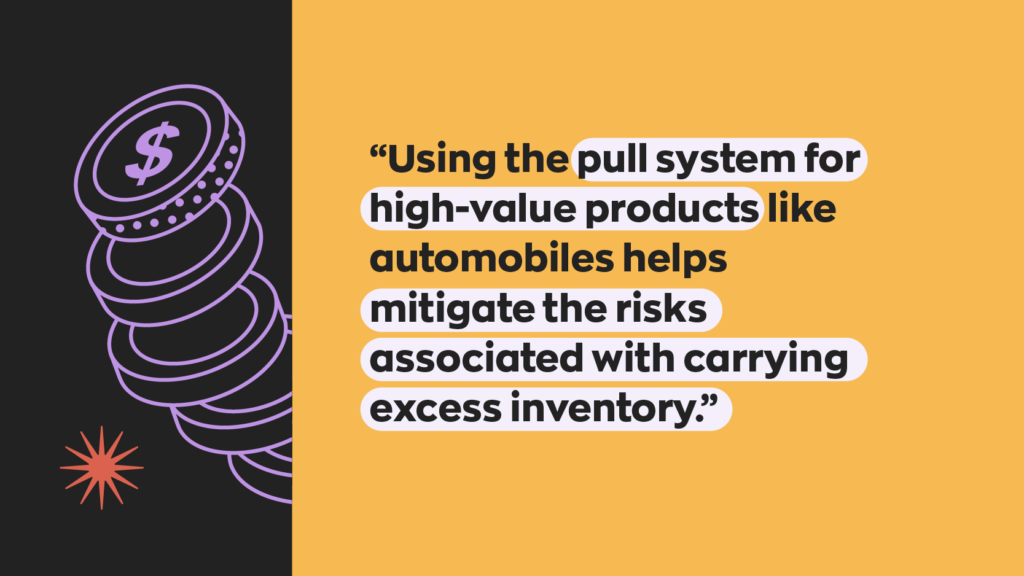
When it comes to food, customers don’t take kindly to empty shelves. If a grocery store were to order as needed, it would quickly lose sales to competitors. Therefore in this situation, it’s better to order in bulk. Considering the cost per unit is significantly lower, keeping the shelves stocked is in the store’s best interest.
Can you choose a hybrid between a push and pull system?
The above example isn’t an exact comparison– a grocery store isn’t really a manufacturer– but it illustrates the point. Both push and pull systems balance risk and reward and require careful management.
There are also hybrid push-pull systems, which seek to reduce the cost of bulk manufacturing while keeping risk low. These hybrid systems flip back and forth between push and pull systems, requiring significantly more upkeep. If you’re looking to implement a hybrid push-pull system, ensure you’re ready– and able– to do so. Not every industry has the flexibility to accommodate such a system.
How can inFlow help?
Like every other manufacturing system, push vs pull systems rely on inventory. Not just knowing what you have on hand but what you can make with it. With inFlow, you can create work orders, and bill of materials (BOMs), allowing you to track everything as it travels through the manufacturing process.
inFlow offers perpetual inventory management alongside automatic updates, letting you know what’s where at any given moment. It also helps you track your manufacturing costs so you can decide between a push vs pull system.
0 Comments