Key takeaways
- Takt time is a concept used to determine the maximum production time per unit needed to meet demand.
- Takt time is a key concept of lean manufacturing.
- It pairs well with just-in-time (JIT) manufacturing and Kanban, which help streamline production and manage workflow effectively.
- The takt time formula is: takt time = available production time / customer demand
- Poor demand forecasting when using takt time could result in deadstock or stockouts.
- Despite technological advances, the core concept of takt time remains the same.
You have to spend money to make money. That’s one of the core principles of any business. You need to pay employees, retain inventory, and fund marketing campaigns to attract new customers. That doesn’t mean that every business spends equally, however. Every business is bound to have its own unique overhead costs, and this is especially true for manufacturers. On average, manufacturers will have higher overhead costs than retailers.
The reason for this is simple. They must source materials, manufacture their product(s) in-house, and then find a buyer for those products. It’s a long, drawn-out, and involved process that demands greater involvement and resources.
For this reason, manufacturers often turn to a strategy known as lean manufacturing. While lean manufacturing has many benefits, it also brings one serious issue: meeting demand. This is where takt time, comes into play.
What is the takt time definition?
Takt time is a lean manufacturing concept used by manufacturers to determine the maximum amount of time available to produce a single unit and still meet demand.
Every business operates according to market demand. Manufacturers are no different and, in many ways, are more susceptible to market shifts. In tandem with lean manufacturing, takt time seeks to provide the necessary pacing to meet demand while avoiding overproduction.
What’s the takt time formula?
The takt time formula is as follows:
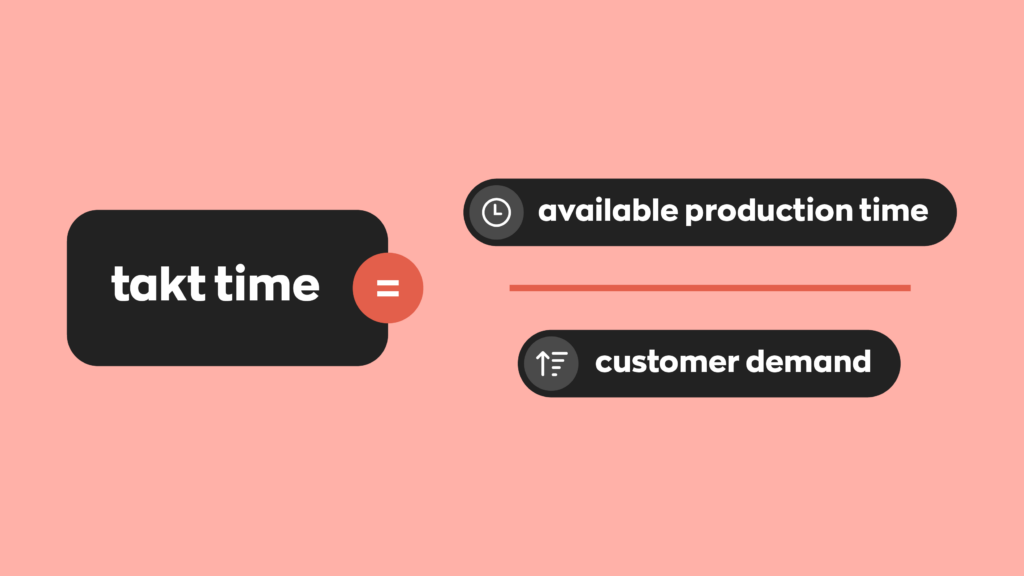
Something important to note is that the unit of time can be anything: minutes, hours, even days, or seconds. The important thing is that it makes sense for your schedule. For example, long production times can sometimes take weeks. In cases like these, it may make more sense to use days as the unit of time.
For the following example, we’ll use minutes.
Let’s say a manufacturer operates 8 hours or 480 minutes a day. However, when using the takt time formula, it’s important to factor in downtime. Most manufacturing facilities aren’t able to operate a full 8 hours with no interruptions. There are employee breaks to consider, and also downtime caused by maintenance. So, for the sake of this example, let’s say there are 6 hours of manufacturing time per day, or 360 minutes. Let’s also say that the average demand is 60 units a day.
Plugging that into the takt time formula, we get the following:
takt time = 360 / 60
takt time = 6
So, in this case, the takt time is 6. This means the slowest production rate to meet demand is one unit every 6 minutes. Pretty simple, right?
While the takt time formula is simple, many variables are at play. For example, we factored downtime in the equation, but those numbers aren’t always as simple to establish. Downtime caused by machine maintenance, in particular, is incredibly difficult to predict.
What are the benefits of takt time?
We mentioned lean manufacturing up above, and that’s not by mistake. Takt time is important enough to merit its own discussion, but it’s not a system on its own. It’s more accurate to think of it as a crucial piece of lean manufacturing.
Lean manufacturing aims to reduce overhead costs, while takt time ensures that the manufacturing process can keep up with demand. Basically, the takt time formula is a tool manufacturers can use to improve efficiency across the board while eliminating waste. This waste could be time, materials, or labor.
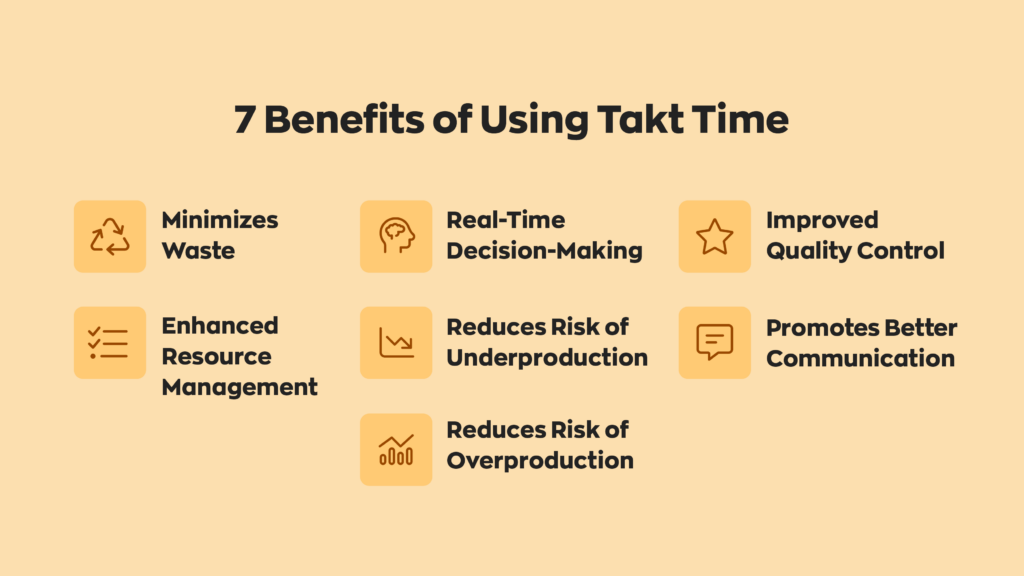
Another less obvious benefit is increased communication since it requires different parts of the business to exchange information regularly. It’s hard to overstate the benefits of regular, more transparent communication.
What does takt work well with?
While takt itself is an important figure– and something you should always consider– it generally works best alongside other strategies. Two notable ones are just-in-time manufacturing and Kanban.
Just-in-time manufacturing
Just-in-time inventory is an inventory management technique that Toyota popularized. JIT manufacturing follows the same principles and is another cornerstone of lean manufacturing. It should come as no surprise that it goes hand-in-hand with takt time. JIT dictates that manufacturers only begin production once they receive orders.
Kanban
Another manufacturing system popularized by Toyota is the kanban method. It’s a Japanese word that translates literally to “signboard.” It refers to a visualization system for work. You can think of it a bit like an Excel sheet. It breaks down stages of tasks into different columns to be completed in order. Ideally, it outlines the entire process from start to finish. Notably, Kanban operates on a pull system. In this production control method, work is initiated only when there is a demand, rather than pushing products through based on forecasts or schedules.
What are the challenges of takt time?
As helpful as takt time is, it also introduces some new challenges. Generally speaking, it requires accurate forecasts. Otherwise, you’ll find yourself on two possible sides of the spectrum: overproduction and underproduction.
- Overproduction refers to manufacturing more units than there is demand for. On the face of it, there are some benefits to this. More product means there’s more to sell, which means higher profits. But like we said above, demand ebbs and flows. Extra stock can become deadstock at a moment’s notice, incurring heavy losses. There are also carrying costs to consider.
- Underproduction refers to manufacturing fewer units than there is demand for. Some situations call for a slower, more controlled production process. For example, companies that manufacture vehicles often take extra care to ensure the quality of their products. However, underproduction to the point where you encounter stockouts is never a good idea.
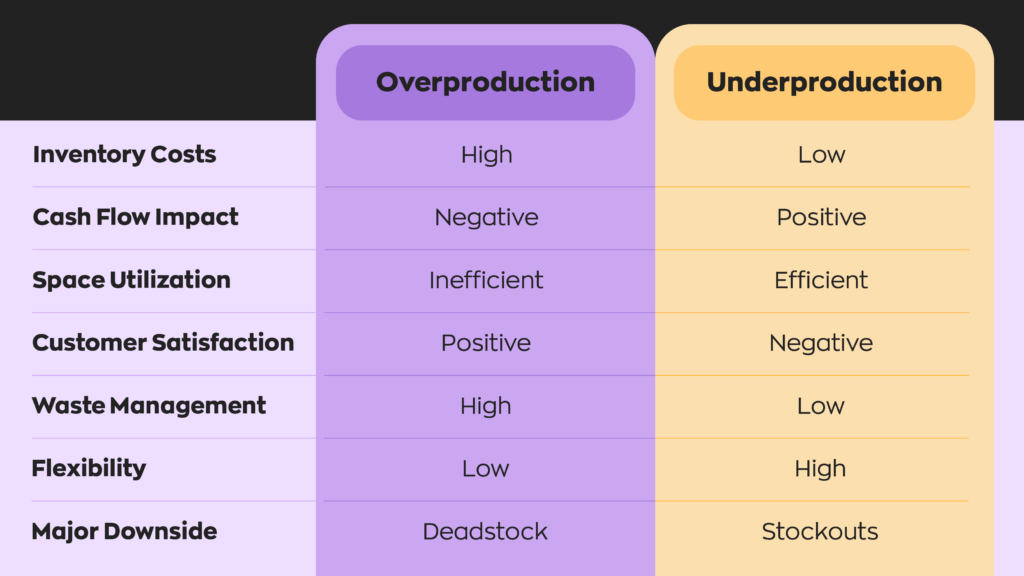
Another challenge with takt time is that it’s not a static figure. As demand changes, the rate of production must change to match it. While calculating takt time is simple, remaining aware of market changes and making adjustments can be difficult.
How has takt time changed?
Takt time has evolved significantly with advancements in technology. Manufacturers are now able to make it more adaptable and precise. Here’s how:
- Real-time monitoring: Modern manufacturing software, like inFlow, enables perpetual inventory tracking, which allows manufacturers to make data-driven decisions. These systems make it easier to adjust takt time as market demands shift.
- Predictive analysis: Demand forecasting has always involved analysis to predict future outcomes, but today, technology has made the process more accurate and accessible. Businesses can now use software to run reports and get loads of relevant data with the click of a button.
- Automation: When most people think of manufacturing automation, they picture big robot arms doing manual tasks. But in reality, most automation is pretty mundane. For example, inFlow has a built-in barcode system, allowing users to generate, print, and scan barcodes. Our software also has reorder points, which automatically track your stock levels and notify you when it’s time to order more.
- Artificial intelligence (AI): While the subject has no shortage of controversy, AI is here to stay. It offers a potential solution for many different problems. It can gather data, organize it coherently, and help form business plans according to that data. Businesses can utilize AI to crunch the numbers and help with their future takt time calculations.
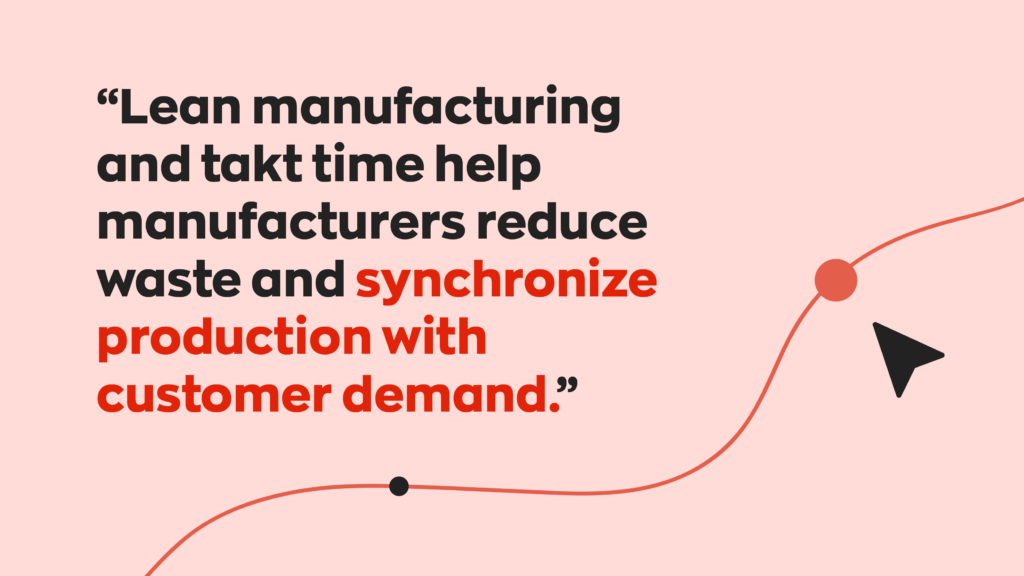
Technological advances will undoubtedly bring more changes to takt time in the future, but its principles remain the same.
Conclusion
For manufacturers looking to employ lean manufacturing, takt time is a crucial component. It helps businesses be as efficient as possible while still meeting customer demand. Although the concept is simple, implementing the takt time formula effectively requires careful planning. You’ll need accurate forecasting and flexibility to adjust to changing conditions.
The bottom line is the takt time formula is a great way to maintain a competitive edge. Manufacturers who understand this metric and apply it effectively will streamline their operations, reduce waste, and foster better communication across teams.
0 Comments