Good inventory management means you have the right inventory available at the right time. However, no matter how well it’s managed, holding stock comes at a cost. In fact, inventory carrying costs could total up to 30% of the value of your inventory.
We take a look at what inventory carrying costs mean for your business, how to calculate them, and where you can make valuable savings.
What are inventory carrying costs?
Costs associated with storing inventory can add up quickly. Some of these are obvious, such as the ongoing cost of a storage facility for inventory that has been sitting around, unsold. But there are many other expenses that can go unnoticed, too. For example, the money you have invested in unsold inventory or the risk of shrinkage.
Carrying costs are these expenses added up and expressed as a percentage of your inventory value. Carrying costs relate to any inventory a business is carrying, even if it will be sold quickly.
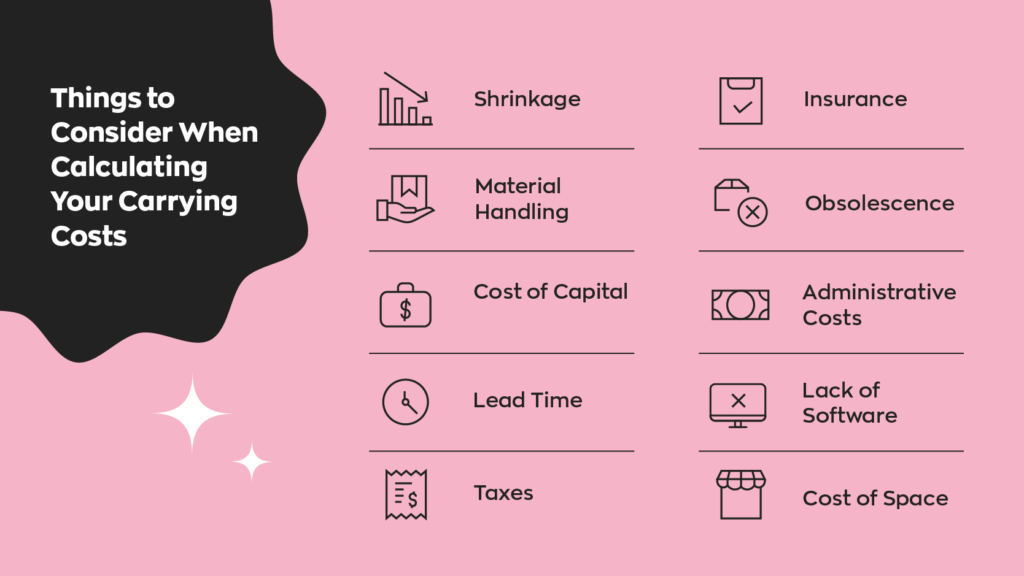
Why calculating carrying costs is important
Good inventory management helps you take control of your business. You can make sure you have the right products, from the right sources, available at the right time. Clearly, this makes for happy customers, which makes for business growth.
However, without factoring in carrying costs, inventory management plans can be unrealistic. These expenses can be 20% to 30% of the value of your inventory. That’s a big number to leave out of calculations and could even mean you don’t have the right overview of your business accounts.
Understanding how much holding stock costs helps accounting teams stay on top of figures. Businesses can then buy the optimum amount, knowing exactly how much they’re spending and what the risks are.
Calculating inventory carrying costs
There are several ways to calculate inventory carrying costs. Some techniques give more accurate results while others give an approximate idea.
For a quick estimate of carrying costs, you can divide your annual inventory total by four. Alternatively, another commonly accepted way to calculate the total is through a carrying costs formula.
Carrying cost formula
When using a carrying cost formula, costs are calculated as a percentage of the value of your inventory. An example formula could look like this:
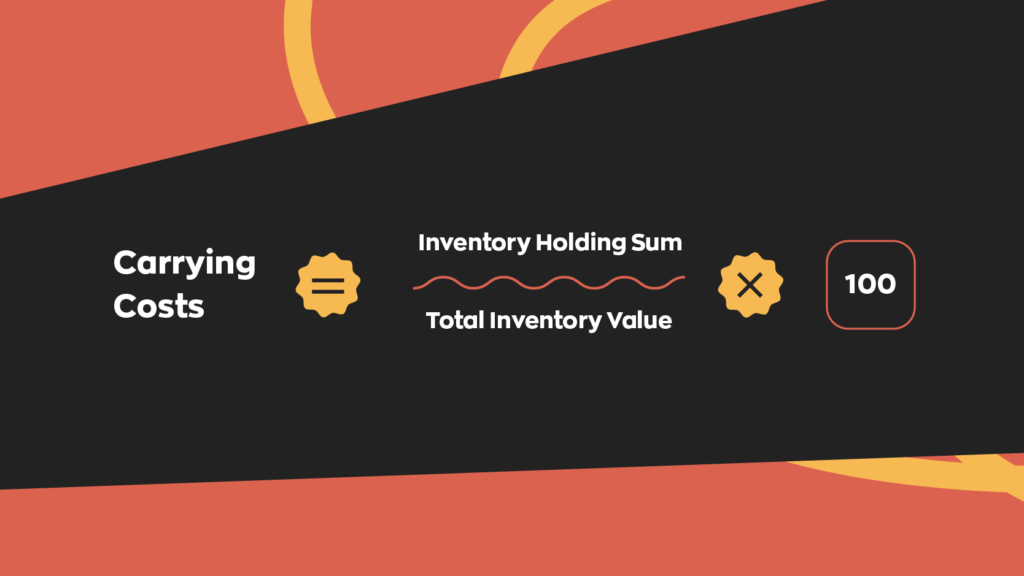
It’s important to note that carrying costs vary between industries and companies, so it’s best to research the right way to calculate your costs, using a formula that works for your business, and ensuring you understand each component.
While a formula might look a little daunting at first, it’s much simpler when broken down into its individual parts. Let’s take a look in more detail at where the inventory holding sum comes from in the above formula.
Calculating your inventory holding sum
Your inventory holding sum is calculated by adding up the total expenses involved in storing your inventory. These can be categorized in a number of ways, but are often broken down into four areas. There are:
1. Capital Cost – This is the money that is invested in your inventory, including interest.
2. Inventory Service Cost – Any costs relating to taxes, administration, material handling, and insurance (fire, theft, etc.) fall into this category.
3. Inventory Risk Cost – Risk costs vary depending on the company but usually cover obsolescence, damage, shrinkage, and relocation of inventory.
4. Storage Space Cost – Storage space costs account for just that: where you store your inventory. These might be fixed or variable costs.
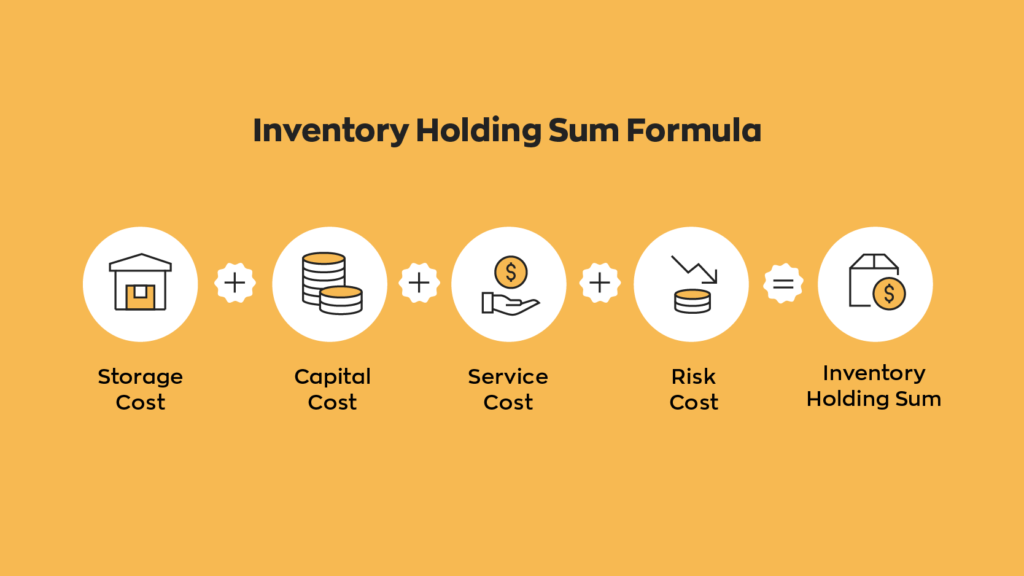
Calculating holding costs and carrying costs: an example
To get a better idea of how you might calculate your carrying costs lets go over a quick example. Archon optical buys 300 frames for their Banshee line of glasses. They paid $1500 for the frames, which sets the price of each frame at $5. Each of these frames has a retail price of $30 which means they’re total inventory value is $9000. Archon Optical also pays $50 in taxes and insurance on their inventory and $150 in storage fees.
It’s important to figure out how much each frame is worth in order to calculate your shrinkage. Shrinkage is one of the factors that can affect your inventory risk cost. It happens when businesses find they have fewer items in their inventory than expected. This might be as a result of theft, damage, fraud, clerical error, or more. For this example we’ll say that Archon Optical lost six frames due to shrinkage costing a total of $35.
Using the numbers outlined above the inventory holding sum of the Banshee frames would be:
$1500(Capital Cost) + $50(Service Cost) + $150(Storage Cost) + $35(Risk Cost) = $1735
Now using the holding sum we can calculate the carrying costs of the Banshee frames, which would be:
$1735(inventory holding sum) / $9000(total inventory value) X 100 = 19.3%.
Can I use an industry average?
For those who aren’t math-minded, calculating inventory costs using formulas like the ones above can seem a little daunting. To save time (and frustration) some business owners turn to industry averages and benchmarks instead.
On one hand, this data might be readily available and easier to work with. On the other, it might not produce numbers that are relevant to your business. This idea is explained in more detail by specialists Bernard J. LaLonde and Douglas M. Lambert through the example of cosmetics.
Imagine a cosmetics company decides to find out their carrying costs using industry averages. Which rival should they take as a model? Should they compare their company to Avon, which sells through representatives or Revlon which sells in major department stores?
Taking an average of both might seem like a good way to cover all bases, but in reality, the company would then be comparing itself to a business which didn’t actually exist. Instead, LaLonde and Lambert recommend that each company determines its own carrying costs, with the aim of minimizing them.
How to reduce carrying costs
Reducing carrying costs is a realistic possibility. In fact, Gartner predicts that, “by 2024, Tier 1 retailers in North America and Europe will reduce inventory carrying costs by 30%”. As the company explains, this could dramatically improve cash flow for digital investments and the state of balance sheets. However, it’s important to plan for success.
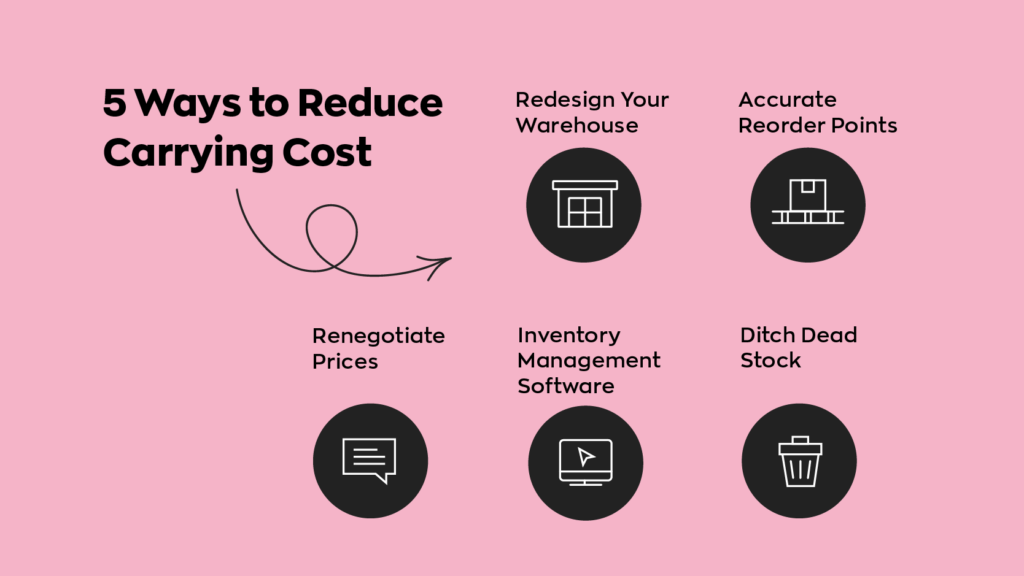
Simply put, businesses need to understand what their current inventory management processes look like and work out how to improve them. One way to reduce carrying costs is to use the right technology. This could be anything and everything from simple, real-time inventory monitoring to high-tech automatic reordering systems.
Inventory management systems
Buying inventory can be a big expense. Finding the best way to manage it means happy customers (because products are in stock) and a profitable business (your costs aren’t unnecessarily high). Using an all-in-one platform can help you streamline everything from purchasing to barcoding to reporting and beyond.
Choosing a system to implement might seem daunting at first, which is why we’ve created a quick guide to help you get started, covering everything from case studies to system types.
Interesting article! I’ve never heard of inventory carrying costs before. I’m definitely going to have to look into this more.
Hey uptoWord,
We’re glad we could provide you with some new and useful information! Be sure to keep an eye out for more blogs. We post content regularly that you may find helpful.
Cheers,
Jared
Thanks for breaking down the concept of inventory carrying costs! I never realized how many factors go into the calculation. This gives me a better understanding of how to manage inventory more effectively. Looking forward to implementing these insights!
Hey Tiny,
Carrying costs can get pretty complicated. We’re glad we could help break them down for you. Thanks for reading!
Cheers,
Jared