Managing operating costs is an essential part of any business. This is doubly true for manufacturers who have a lot more variables to consider. On top of typical operating costs– wages, electricity, warehouse space, and so on– they have to deal with sourcing raw materials. But these costs are not static. They naturally change over time due to a variety of factors. This is why the direct materials cost variance formula is so important.
This commonly used formula is crucial to how businesses determine their cost variance to ensure they remain operational. You could also use it to identify which areas can make use of cost-saving measures, leading to greater overall profits.
If you’re interested in more useful inventory-related formulas, you can check out our free Inventory Formula Cheat Sheet. Download your inventory cheat sheet now!
Today, we’re talking about the direct materials cost variance formula, and there’s a lot of things to cover, so let’s roll up our sleeves and get down to business.
What is the direct materials cost variance formula?
Aside from being a mouthful, the cost variance formula is exactly what the name suggests. It’s a mathematical formula that manufacturers use to calculate cost variance. That might sound confusing, but as we’ve established, the cost of materials is not static. It can change drastically within a short period.
If all you’re looking for is the formula, here it is:
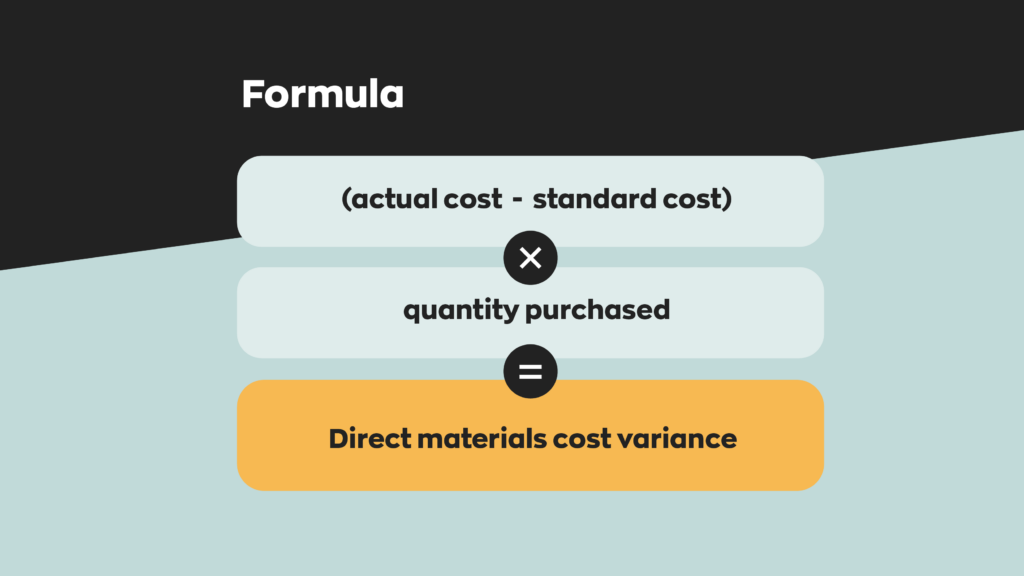
Now, let’s take a closer look at the formula’s components.
Standard cost
Because the cost of materials varies over time, the accounting department sets an ideal price for certain materials. This is the standard cost and, ideally, the highest price a manufacturer pays for materials. If you can get it for less– great! However, keep in mind that sometimes spending a bit more also buys better quality.
Sometimes, you just won’t be able to get inventory for the standard cost. In those cases, keeping products on the shelves is more important than waiting for a better deal.
Actual cost
The actual cost is exactly what it sounds like. It’s the price that the business actually pays per individual good. Sometimes, buying at standard cost just isn’t possible, and sometimes, a better deal comes around.
If the actual cost is less than the standard cost, don’t worry about the negative number. We’ll talk about that more later.
Using the direct materials cost variance formula
Now that you know what the direct materials cost variance formula is, you need to know how to use it. It’s easy enough to plug it into a calculator, but having hands-on understanding is much more valuable.
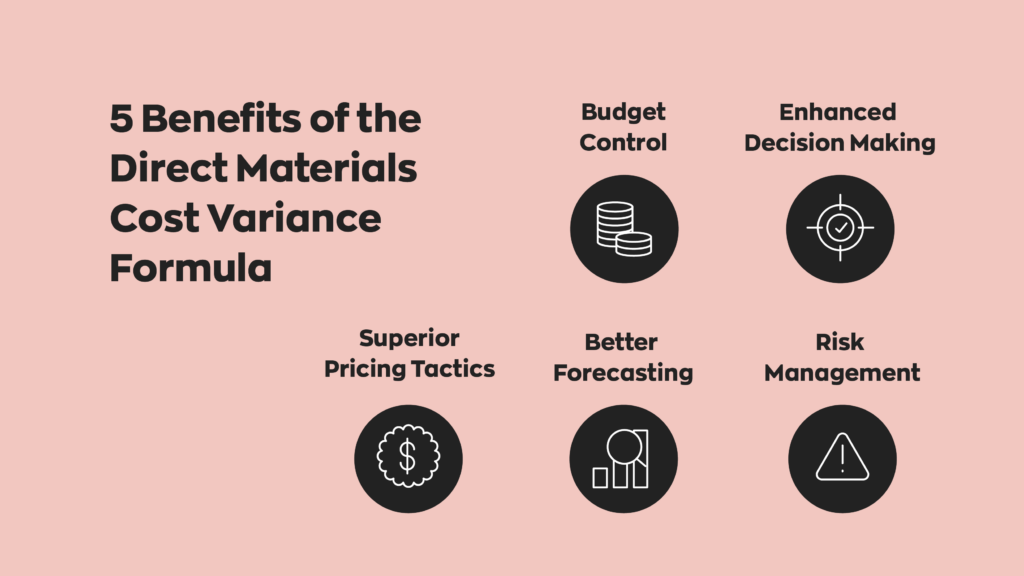
For this example, let’s pretend you’re a small furniture manufacturer specializing in oak rocking chairs. Now, let’s say that you’re in the process of ordering 500 units of oak wood. Let’s also say that the standard cost of oak wood units is $5/unit. That means that the standard cost for this shipment is $2500.
Unfortunately, the lumber market is still recovering from the effects of the pandemic. As a result, you can’t find any sellers offering less than $7/unit. Remember– keeping products on the shelves is more important than sticking to the standard cost!
That means the actual cost for this shipment is as follows: $7 x 500 = $3500.
For now, you can discard the $2500 and $3500 formula. We’ll be using the cost per unit for the formula. But keep in mind the difference between them is $1000.
The direct material cost variance formula in action
Now that you have all the necessary numbers, you can plug them into the direct materials cost variance formula. Here’s what it looks like:
Direct materials cost variance = ($7 – $5) x 500
Direct materials cost variance = ($2) x 500
Direct materials cost variance = $1000
So, in this case, the cost variance is $1000. That lines up with the difference in cost. This seems simple when dealing with small whole numbers but gets more complicated with larger numbers and more realistic prices.
A good general rule regarding direct materials cost variance is that positive numbers are seen as “unfavorable” while negative numbers are seen as “favorable.” Some businesses flag certain thresholds for their procurement teams to watch for.
Using the example above, let’s say you ran the numbers and found that you can’t buy materials priced more than 50% of their standard cost for your furniture business to stay profitable. With this information, your employees will know to avoid purchasing materials when priced beyond these thresholds unless absolutely necessary.
While number crunching, you also found that your materials never go on sale at more than a 50% discount. If your team sees materials priced this low, they will know it’s an excellent time to restock and maybe even get a little extra.
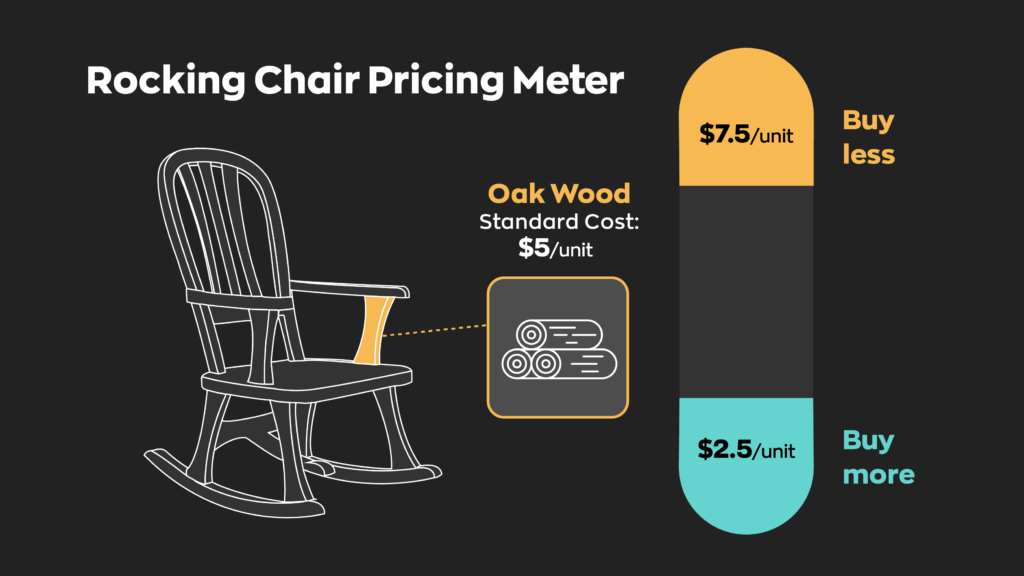
Why is cost variance useful?
It might be hard to gather enough information at first to estimate accurate standard costs. But over time, as you purchase more and more materials, you’ll collect more data points, and eventually, you’ll be able to average out these data points. While it’s still a rough estimate, it can offer a decent idea of what you’ll be spending on materials. This makes planning easier and means businesses can allocate capital to other areas of the business.
Aggregating data points also gives a good idea of what a “good” deal is. This might not sound like much, but purchasing in bulk when the market is down means more savings in the long run. It can also help predict market trends, potentially saving businesses from buying when prices are abnormally high.
Why does cost variance happen?
To an extent, cost variance is a natural occurrence. Market changes are normal and occur due to a number of different variables. Scarcity is the obvious one, but there are also less visible factors, like inflation and exchange rates. These are constant factors that are always at play, which makes them relatively easy to account for.
At the same time, sometimes, world-changing events change things drastically. No one thought we’d ever live through something like the COVID-19 pandemic, but here we are. Now, businesses go out of their way to account for such events. We’re not saying that you have to– it depends on the industry– but it’s better to be safe than sorry.
What tools help determine cost variance?
We touched on this briefly, but aggregating data is a big part of using the direct materials cost variance formula. And lots of it. It’s possible to do all of this recording and calculating by hand or using spreadsheets, but it’s incredibly inefficient. In the long run, it’ll usually cost more than it saves.
Our software inFlow makes recording, aggregating, and calculating your direct materials cost a breeze. We put some great reporting features into inFlow so you can get all sorts of valuable data points with just a few clicks. The result? Easily accessible data that’s laid out in an easy-to-understand manner.
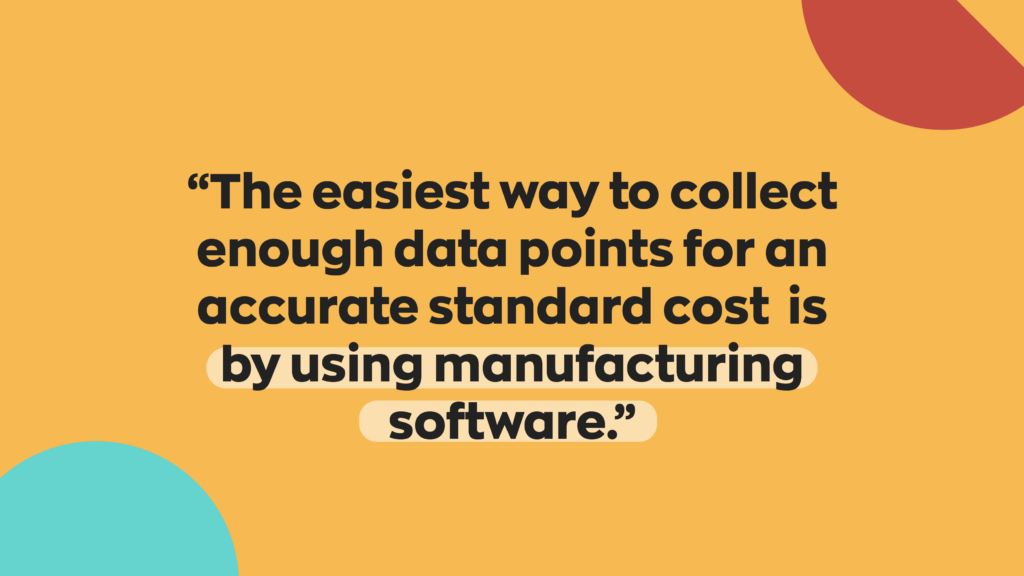
While we’re proud of the reporting features we’ve put into inFlow, they’re far from the most valuable thing manufacturers will get from our software. We recently did a huge manufacturing update that added all kinds of features manufacturers need, like manufacture orders, auto-building after a sale, and more easily estimating build costs, to name just a few.
So, if you’re a manufacturer looking for well-rounded manufacturing software, look no further than inFlow. We know you’re going to love it.
0 Comments