When we say multi-location, you probably think of chain stores like Wal-Mart and Target. Maybe even Costco. Retail juggernauts with many locations across many different cities, states, and even countries. However, multi-location inventory management is a necessity for medium-sized and occasionally small businesses as well.
So: what is multi-location inventory management? When does your business need it? What are some things to keep in mind when implementing a multi-location system?
What is multi-location inventory management?
As the name suggests, multi-location inventory management is the practice of managing inventory across more than one location. There’s a lot of reasons a business may do this. The most obvious one is if your business has more than one location, you (usually) need more than one storage location.
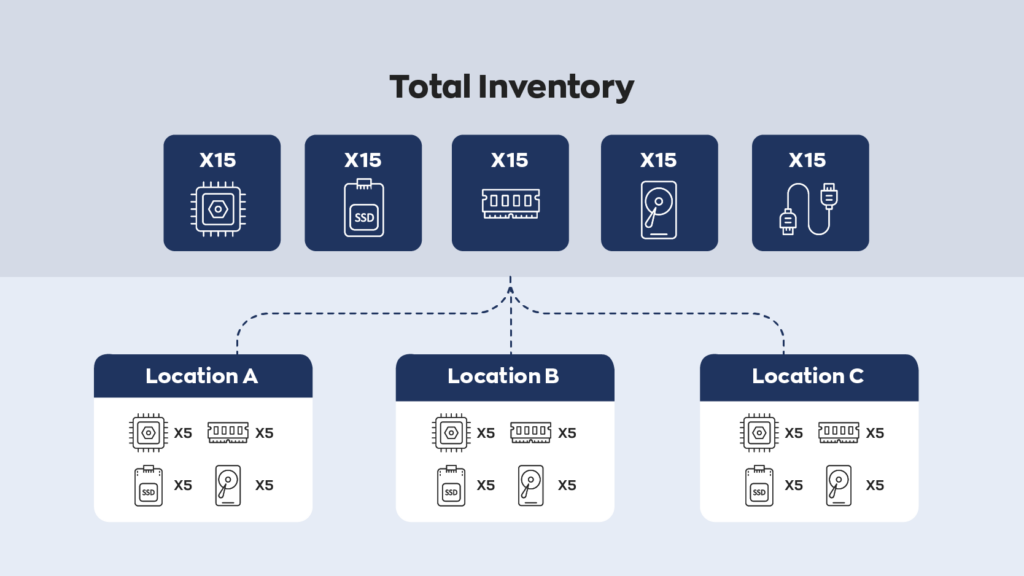
Why is multi-location inventory management important?
Renting another warehouse or storage crate might sound more expensive, but it cuts costs elsewhere. Having a nearby location to pull inventory from can save on shipping and labor costs. In some instances, it can also be cheaper to rent two smaller warehouses than one massive one.
When do you need multi-location inventory management?
If a business has more than one retail location, it usually needs another warehouse. There’s some exceptions– if both locations are close enough, you can sometimes get away with just one warehouse. However, close proximity like this can lead to other issues.
For example, if both locations are too close to each other, they’ll end up competing with each other for business. This is fine for large retail chains with billions of dollars backing them up but not for smaller businesses that run on finer margins.
There are also more nuanced instances where multi-location inventory management makes sense. If a business carries many different products of different sizes, it could be worth separating them in different warehouses. The closer warehouse would store the higher-demand products, while the further one would store lower-demand products.
This makes it easier to keep up with demand as long as you can manage things correctly. However, instances like this are the exception rather than the norm.
What about industry differences?
Some industries may also place greater value on a multi-location system. Practitioners of lean manufacturing, for example, can send their products through different sites where each one performs a different task. This helps them keep better track of the manufacturing process itself and further helps manufacturers compartmentalize different parts of the business.

Challenges of multi-location inventory management
If all of this sounds complicated, that’s because it is. Managing inventory on a single site already has a lot of intricacies. Switching to a multi-site system directly multiplies the intricacies that a business has to manage. And because sales depend directly on inventory, messing something up can cause a lot of damage. And, of course, managing multiple locations introduces entirely new challenges. Here’s some to keep in mind.
Proper tracking and management
This is the biggest challenge, as well as the most obvious one. Because tracking inventory at one location can already be difficult, switching to multi-location means that the difficulty is multiplied. Additionally, because product units of the same type generally come from the same supply line, a mistake at one location usually means a mistake at another.
Managing supply chain logistics
On the other hand, very few businesses carry only one or two products. The more products you have, the more supply lines you need. And when you introduce multi-location inventory management, those new locations require supply line modifications. As a result, you’ll have to organize new shipping routes, which in turn requires redistribution of manpower.
Communication between multi-location sites
This challenge isn’t as tangible as the ones above, but it’s still a large factor. Despite being in different areas, the goal of multi-location sites is to increase the number of sales. That means communication between the two sites is important to minimize the fine details.
Bottlenecks
While more of an issue for manufacturers, bottlenecks continue to be a relevant issue for businesses around the world. When products don’t move quickly enough, it backs up the entire supply line. Everything slows down, and because multiple sites mean more overhead costs, it’s a bigger issue for multi-site systems.
Proper allocation of product
The number of sales between different sites will naturally differ. This is due to a number of external factors outside of your direct control. Things like environment, culture, location, and so on. This means that, in theory, there’s a perfect allocation of products between locations. In practice, though, it can be difficult to find the proper allocation. If you allocate too much to one site, you risk losing sales on the other. The same applies to allocating too little to one site.
Multi-site inventory management best practices
The basics of inventory management are the same for multi-location systems. But, there’s enough differences between the two that figuring out where to go can be difficult. Here are some tips and tricks to help set the foundation for a proper system going forward.
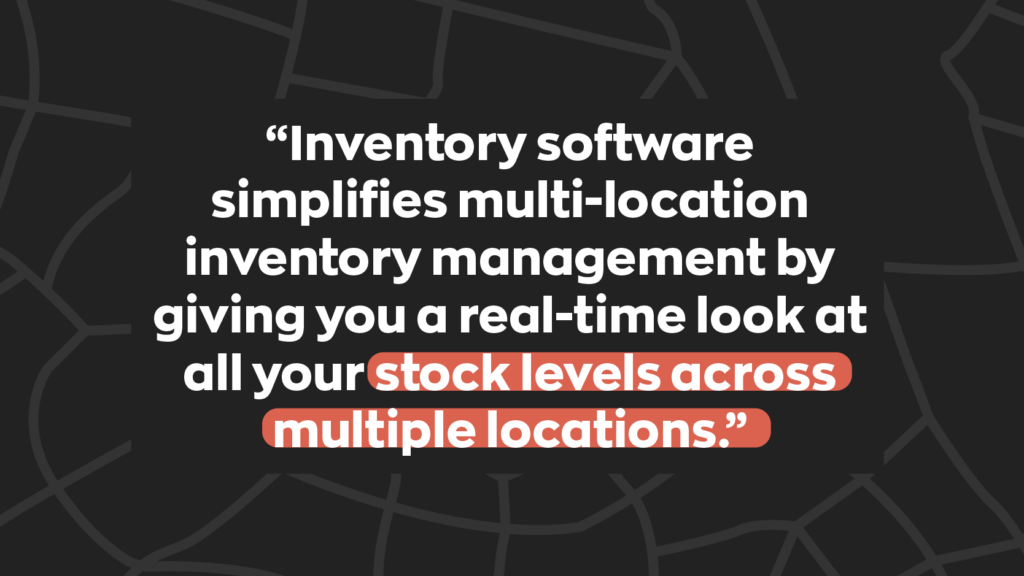
Implement multi-location inventory management software
Some single-site businesses manage their inventory by manually updating a spreadsheet. It’s one possible avenue, but it’s also terribly inefficient and prone to error. Trying to do that for multi-location is even worse. Using software like inFlow to keep track of everything– including invoicing, inventory management, and supply lines– goes a long way in cutting costs elsewhere.
Utilize safety stock and reorder points
We touched on this above, but allocating products is a delicate process. Too little to one location results in a loss of sales. Too much, and you’re spending more on overhead. This is where reorder points and safety stock come in handy. Safety stock will cover you for those “just in case” moments and reorder points will ensure you order the right amount of products at exactly the right time. With inFlow you can set up reorder points for each of your products so you’ll be notified when it’s time to order more.
Consider demand at each location
It’s impossible to forecast demand completely accurately, but it’s possible to get a fairly accurate estimate. Use these estimates when deciding how many units to allocate to each multi-location site. Proper allocation will result in greater profits and lower overhead costs. This is another area where software like inFlow can help. With inFlow’s robust reporting, you can get a glimpse at how your inventory is selling at each location. This will allow to to make more informed decisions when stocking your inventory.
Wrapping up
Multi-location inventory management is an incredibly important part of any multi-location business. It ensures that products stay in stock, supply lines remain steady, and that revenue keeps flowing.
At the same time, however, managing inventory across multiple locations can prove rather difficult. It’s best to take advantage of new-age perpetual inventory systems like inFlow so you can track things automatically. There’s a reason we were rated #1 on Softwareworld’s list of top inventory management software.
0 Comments